Introduction
On this occasion, we've had the chance of speaking to one of the engineers in charge of designing sailboats for two of the toughest and most prestigious sailing competitions of all times; the Volvo Ocean Race and the America's Cup. Britton Ward, Vice President of Farr Yacht Design has given us some thought-provoking and fascinating insight into the aerodynamics of sailing.
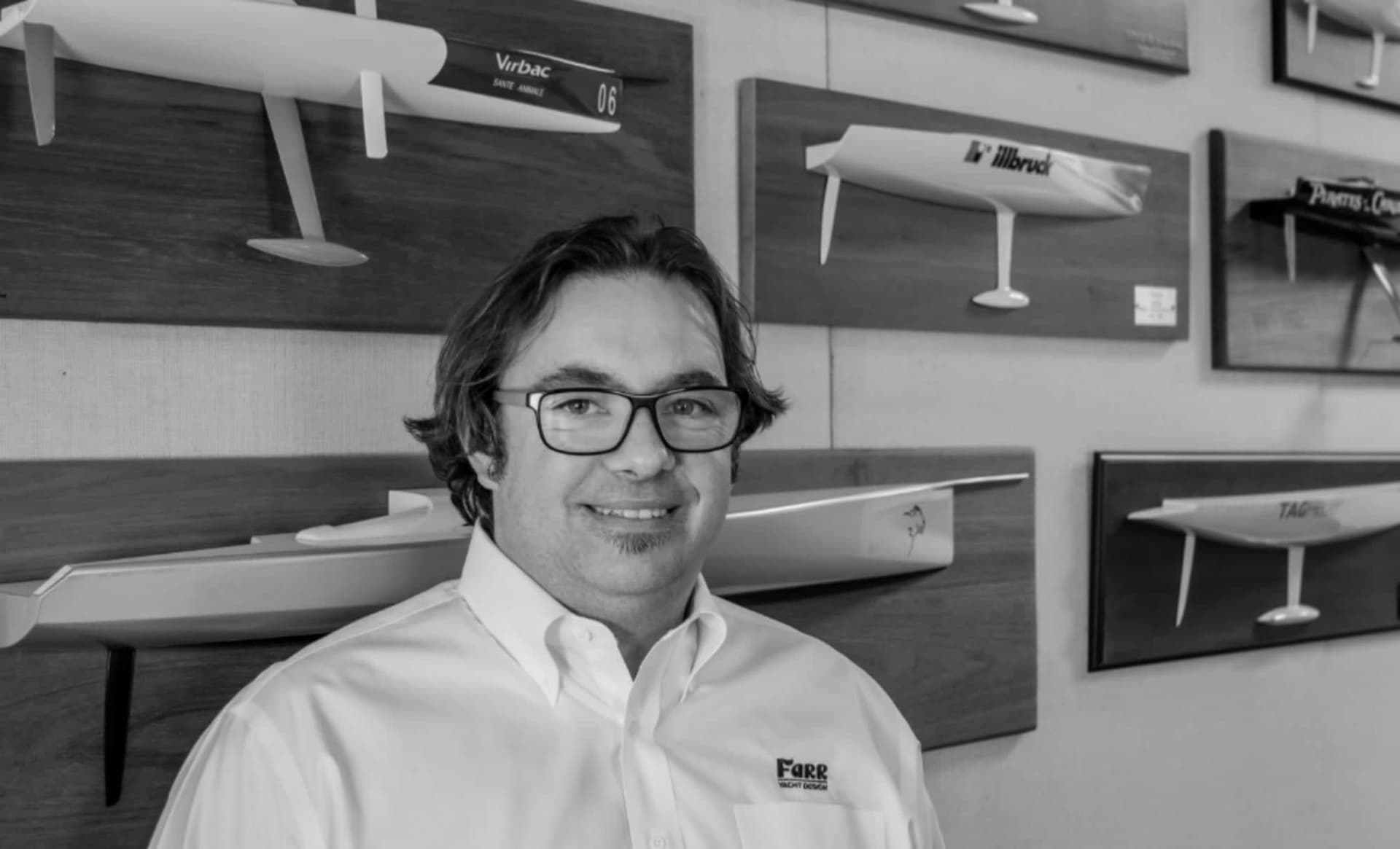
Setting sail towards a Childhood Dream
To put things into context, talk me through your career path and how you got into this industry? My name is Britton Ward, I'm Vice President and Senior Naval Architect at Farr Yacht Design in Annapolis Maryland, USA. My fascination with sailing yachts happened at a young age. Growing up in Western Australia I was completely enthralled by Australia II's America's Cup victory in 1983. The 1987 Cup defence was in my home Fremantle waters and from that point on I knew I wanted to be involved in designing racing yachts. I attended the Webb institute of Naval Architecture in New York and followed that with a master's degree from MIT. From MIT I joined Farr Yacht Design and have been lucky enough to work on a wide range of projects including 4 America's Cups, Volvo Ocean Races, grand-prix racing projects, cruising boats and a number of high-performance powerboats.
Aerodynamics in Yacht Sailing
Throughout these years have you seen a significant change on the aerodynamics side of competition? Yes, what makes sailing design so unique is that we have to operate across such a wide range of operating conditions; from no speed to 30,40, sometimes 50 knots, upright and at heel and at different angles of sideslip or leeway. The designs must work across a really broad range of conditions which makes simulating every aspect very demanding. The second part is that we are in perhaps the ultimate efficiency game, trying to maximize aerodynamic drive forces while remaining always on a quest for minimum hydrodynamic drag. So, we are constantly trying to improve both the hydrodynamic and aerodynamic sides of the performance equation. Given water density is 800 times that of air, we work really hard at hydrodynamic optimization trying to reduce drag but the sails are our engine and so improving aerodynamic drive and minimizing aerodynamic parasitic drag is critical to achieve maximum efficiency. We work with sail designers in analysing sail shapes and we put a lot of effort into reducing windage by shaping hull and deck surfaces. At the highest end, in America's Cup programmes we have looked at the effect of having a rope in front of the mast for the windage gain or shaping of bowsprit sections to achieve aerodynamic driving force. With the recent push into hydrofoiling yachts that achieve speeds of 40 to 50 knots, the importance of reducing windage drag has become ever more critical and is getting a lot of focus.
In terms of all these features and challenges you have tried to improve, tell me about the design cycle of these sailboats. The challenge is whether the team can support enough R&D to do multiple design refinement cycles using high fidelity tools; whether that be tow tanks or wind tunnels or CFD. For a lot of our regular designs the design budgets and timelines can't support unlimited research, so we work to leverage our existing databases, use empirical methods and perhaps validate with some limited simulations. Whether it is empirical models or experimental data or simulation results, we use different techniques to build Response Surface models that characterize the hydrodynamic and aerodynamic forces acting on the boat, appendages and sails across the range of operating conditions. These models are then used to predict the performance of the boat using a Velocity Prediction programme that can be either 'steady-state' or for very high end projects a full time domain simulator that allows the boat to be sailed virtually. We can then couple that information with expected race conditions or race simulations and begin to optimize the design for the targeted conditions. We have invested heavily in an automated design analysis system called IDEOS that brings together a lot of these elements and automated shape morphing and generation to allow us to look at 1000's of design options before committing to final design. Even with the most complex simulations and computing we are a long way from a black box design process. Anything the computer spits out needs experienced eyes that understand both what's 'under the hood' in the codes but also appreciates real life sailing complexities that aren't able to be fully captured in models.
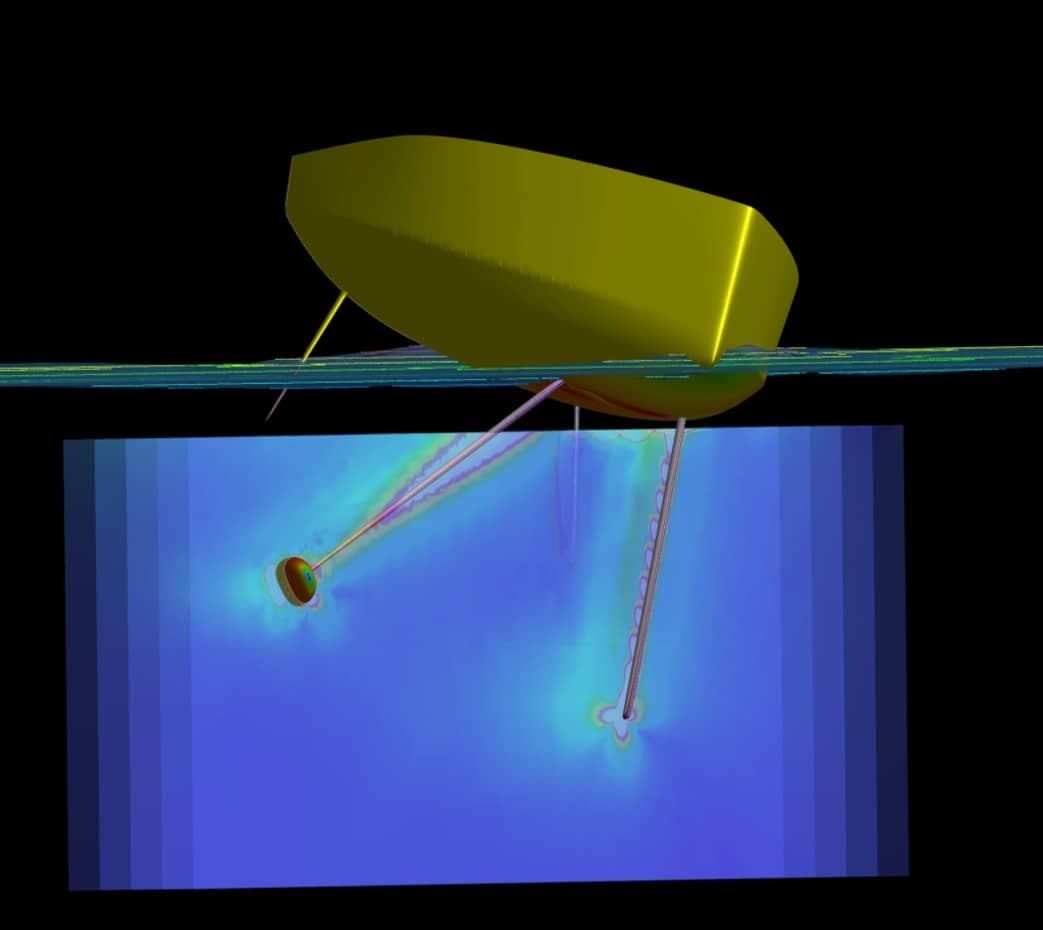
With regards to quantifying and modelling the interaction of different components, what impact does the pressure difference from the main sail have on the entire aerodynamics of the boat? Like in most industries, one starts with computationally simple things, just analysing a set of sail geometries in the air without the presence of the mast, rigging, hull etc.. For sailing at low apparent wind angles with minimal separation we can use Vortex Lattice or Panel methods but at wide angles with spinnakers we have a much more complicated flow regime requiring RANS and in some cases DES simulation to properly capture the flow. Modelling only the sails misses the interactions with mast, rigging, hull and deck which can have a really big impact on the forces and the flow field physics. Much as with hull hydrodynamics we always want better and better accuracy but also need to run a lot of operating conditions to properly model how forces change in different conditions. Every design team needs to find the right balancing act here that can capture as much physics as possible but provide enough data to answer the design questions.
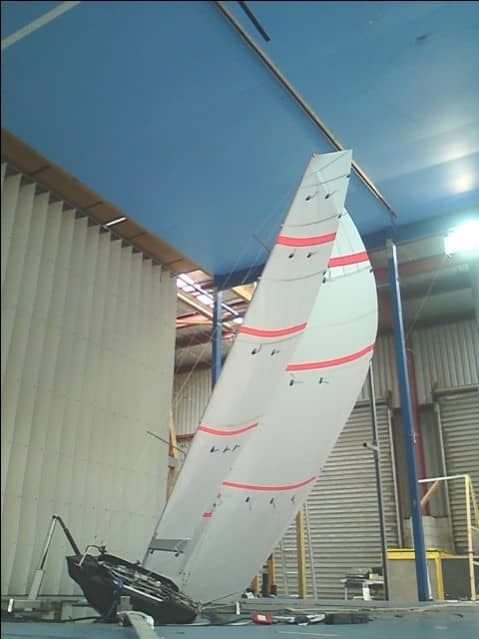
To what extent is it worth developing these foiling sailboats if cavitation effect comes into play at high speeds? The shift to foiling sailboats has dramatically changed the performance zone for these types of boats. Hydrofoiling is not new but the advent of advanced materials has allowed us to achieve exceptionally light weight and strong boats that can be lifted clear of the water by hydrofoils even in quite light conditions. At a basic level hydrofoil design is the same as airfoil development but we are operating in a much more dense fluid. With the foils supporting the boat the total drag is reduced dramatically as the hull is now in the air and so aerodynamic efficiency becomes even more critical. At the higher speeds the low pressure on the foil can drop below the vapor pressure of water cause the water to 'boil' or cavitate and this phenomena tends to govern the upper end of the speed range. Its fundamentally related to the pressure at the foil and the minimum pressure coefficient, if that exceeds the vapour pressure, the water boils. The question is, how do we reduce that? Generally, a bigger foil will have a lower loading on it, which will delay cavitation, but it also has more drag. You are kind of flirting on that cavitation edge or looking for solutions that are somewhat benign to cavitation.
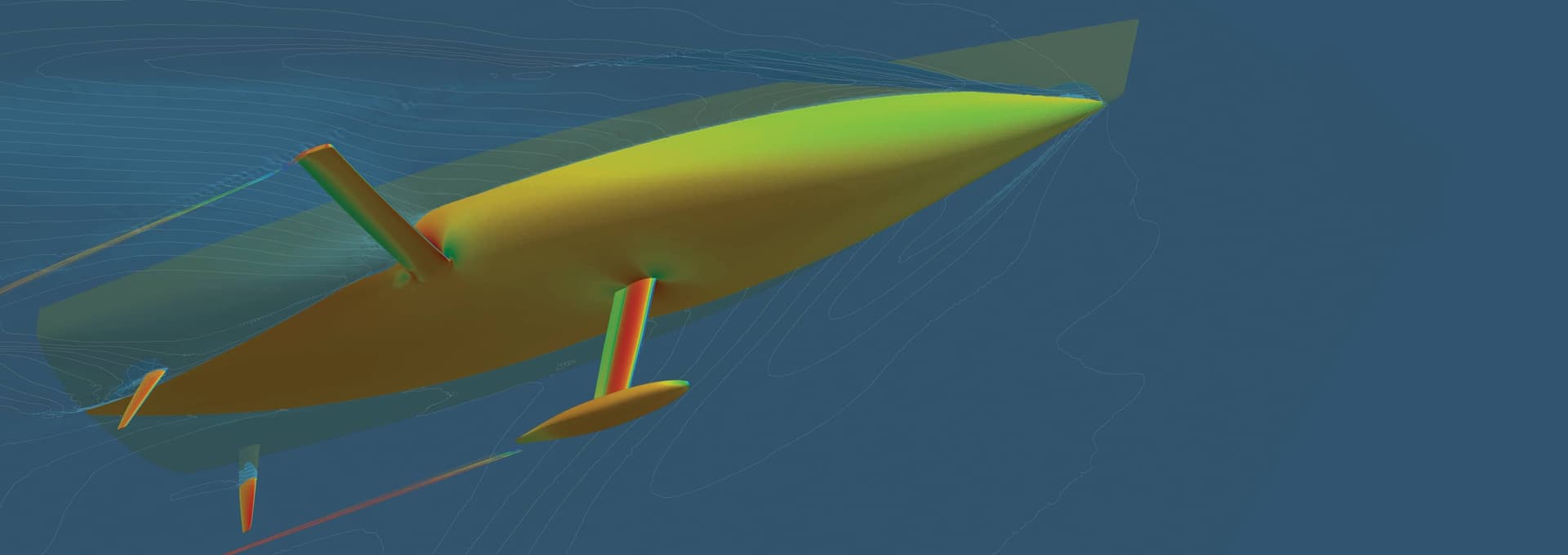
Essence of Competition
Are there any limitations dictated by competition or regulations that limit aerodynamic design freedom? Yes, in America's Cup, for the current AC75 specifically there is a rule that governs the parameters of the boat in a similar way to Formula1. These rules control dimensions, materials and construction processes and the number of components of different types that can be built. It also prescribes limits on control system etc. In the current rule it precludes the use of towing tanks and wind tunnels, requiring design optimization to be completed using only simulation-based analysis.
I see that there is a strong similarity to F1 sport. Recently F1 has been forced to prove itself useful for the general industry, have you felt that there is the same sort of pressure on America's Cup? Everyone involved feels that there must be some trickle down of technology to the average sailor, and there is always a big debate about how much technology will trickle down from the current America's Cup boats. There are certainly a lot of design processes and tools that can be immediately applied to all manner of boats. Refinements in deck hardware and mechanical systems always feed into a range of boats.
How many engineers are dedicated to aerodynamics within the teams? Every company organises itself in different ways so the way we are structured is probably a bit different to other companies or teams. Depending on the scale of the project we would typically have dedicated one or two guys to the aerodynamics in general, and one of those may be heavily involved in the sail design area. Fundamentally the hydrofoil is an airfoil wing, even if it is operating in water so all of the aerodynamics expertise is directly relevant and we use a lot of the same tools and methodologies. In our team we have often had naval architects working with aerospace engineers and I always find it is important to cross-pollinate from different disciplines.
Iconic Designs
Tell us what is so special about the VO65? VO65 was designed for the Volvo Ocean race, which is a fully crewed race around the world race. The VO65 is a one-design boat in which each of the boats are as identical as possible. This was a big change from prior races where they utilized a design rule and each team employed designers and sought to find a design edge. In the 2011-2012 Volvo Ocean race the boats were designed to the VO70 rule and there was a lot of design freedom but also a tendency to push the limits which resulted in a lot of breakages. Thus given the economic situation and the issues in 2014 the race organizers felt that best option to insure the future for the race was to have a fleet of absolutely identical boats and we were commissioned to design the VO65. The main directives for us were to make the boats robust and reliable, as identical as possible. We sought to get as much performance as we could but without sacrificing those core factors. There was limited amount of budget for research and simulations which we utilized to explore some appendage options and develop refined performance predictions. We utilized our internal methods to refine the boats windage characteristics but were not able to complete a lot of detailed aerodynamics refinements. We worked closely with the sail and mast design teams in the sizing of the rig and selection of sail sizes, trying to develop the sail wardrobe to be as solid as possible.
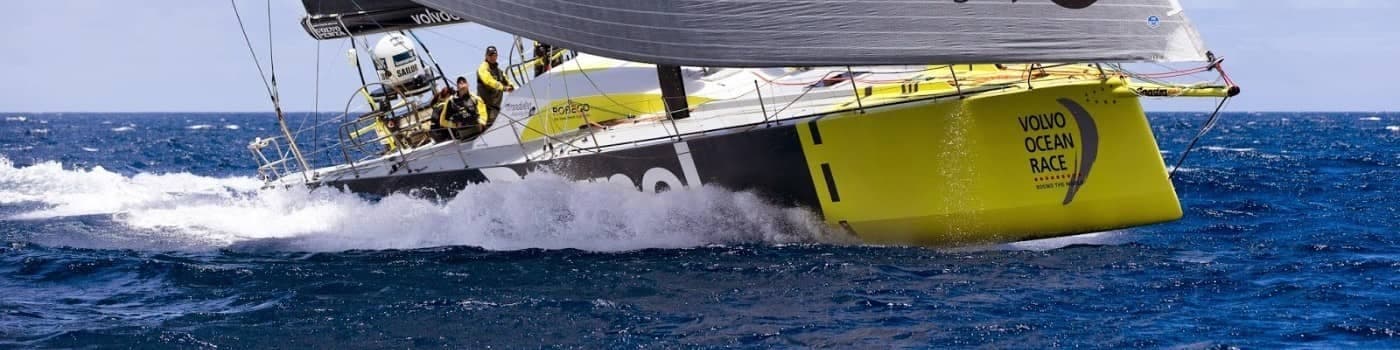
This was back in 2012, but what are the main areas of improvements currently in 2020? The next ocean race will start in 2022, having two classes, the VO 65 and the IMOCA60. Much like the older VO70 rules, the IMOCA60 is a development class, having a core set of rules but allow a lot of design freedom. The boats are now employing hydrofoils as well which has resulted in large performance improvements. In this case, they are not fully airborne as in America's Cup boats, but the foils lift most of the hull clear of the water so are perhaps better seen as 'foil-assisted' boats.
Technical Insights
What is the actual difference between foil assisted and fully flying? Primarily, the IMOCA60 is not allowed to have a tail elevator, so there is no T-rudder, and it uses passive hydrodynamics to maintain 'stable' flight. A big push in that design space is both on sizing and placement of the foils, and in developing a pitch-stable boat across the speed range that while still meeting all the stability and safety rules for an ocean going yacht. The IMOCA60 is an exciting design arena right now as there are a lot of areas to explore and optimize; how much stability you need from the hull design, from the appendix, keel or bulb, the size of the foils; There is plenty of room for a big leap forwards, since there is so much latitude to explore, but typically these budgets are much smaller than America's Cup ones so you have to have bright people and a good understanding of the constraints to make an improvement.
You previously mentioned pitch-wise stability, are there any similarities to the oscillatory modes present in aviation? Yes indeed there are, in aeroplanes it is the phugoid mode, in powerboats we call it porpoising and it is a dynamic instability. A lot of work has been done in the power boats along the years to understand what characteristics of a hull shape make it more or less susceptible to porpoising. Much like an aeroplane, the position of the centre of gravity relative to the hydrodynamic centres is an important part of it. When we come to foil assisted sailboats, this gets even more complicated as we have the extra influence of the hydrofoils changing the boats attitude and varying dynamically with speed. Even in some of the initial simulations I have been doing in the last 6 months with some of my team, we have seen some configurations which appear to be pitch unstable and requiring a bit of trial and error, to understand the right combinations of running trim, foil sizing and placement and centre of gravity position. Now we are coming up with a design methodology using lower fidelity simulation methods to give us immediate guidance on whether a particular design configuration is going to be stable or not.
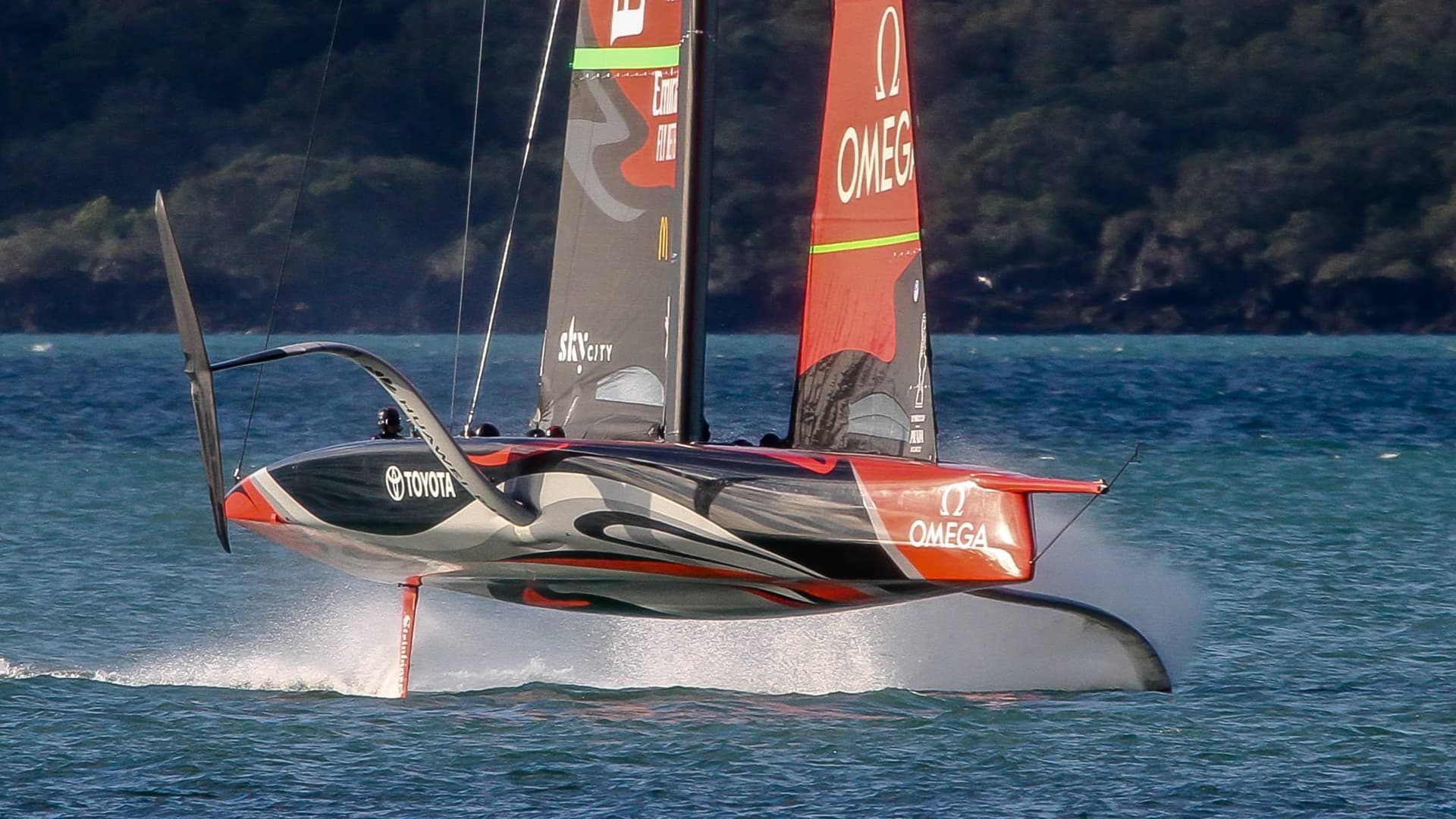
Does the actual position of the crew significantly impact the aerodynamic efficiency and separation points? In any of our designs we focus on crew placement, for their center of mass impact, their ability to ergonomically complete their tasks and for their impact on windage and aerodynamics. Depending on the size of the boat, the weight of the crew has a big impact on the stability of the boat. A smaller boat, the crew weight is a much larger proportion of what the entire boat is, then thus greater impact on resisting the sails and tipping the boat over, therefore you automatically have a trade-off between aerodynamics and crew righting moment.
When you get to a boat like the AC75, the speeds have gone up so much, the aerodynamic impact of the crew is even more significant while the impact of the crew weight on stability of the boat is much smaller. As a result, we see the crew essentially 'buried' in tunnels with their heads down to be as streamlined as possible.
On Course for a Bright Future
What are the projects you have in mind in the near future? We are marching down this path of hydrofoils, not just for racing, but also for cruising boats. We recently launched 142-foot cruising boat with a 9-meter Dynamic Stability Systems hydrofoil. The addition of the foil improves performance and reduces heel angles by up to 15+ degrees while improving pitch motions which dramatically improves crew comfort. I think we are seeing other avenues where these technologies can be applied. Placing a foil in a 142-foot superyacht was a big challenge and one of the hardest projects we have done recently. This was a sliding foil, one foil works on both sides, so it has to be actuated and pulled in to the boat and put out the other side, when the boat tacks. Because this boat will sail the globe we needed to do a lot of assessment of damage possibilities to ensure the boat would be safe in the event the foil collided with something. On a simulation front I am always trying to utilize more simulation tools in all of our designs. Recently we have done a lot of work with OpenFOAM, also Numeca's Fine/Marine primarily for hydrodynamic simulations. We also make a healthy use of panel methods and vortex lattices, X-Foil and XFLR5, depending on the types of problems we are looking at. Since we need so much data in order to make an informative design choice we are always trying to balance fidelity versus run-time. Just running one point of one geometry teaches us very little, so we are constantly looking at ways to use advanced statistical fitting techniques to make the most value out of the data we get from simulations and apply it to broader answers. Beyond that, we have been putting a lot of focus into the automation of design cycles; all the way from geometry morphing though to meshing to running simulations and post processing.
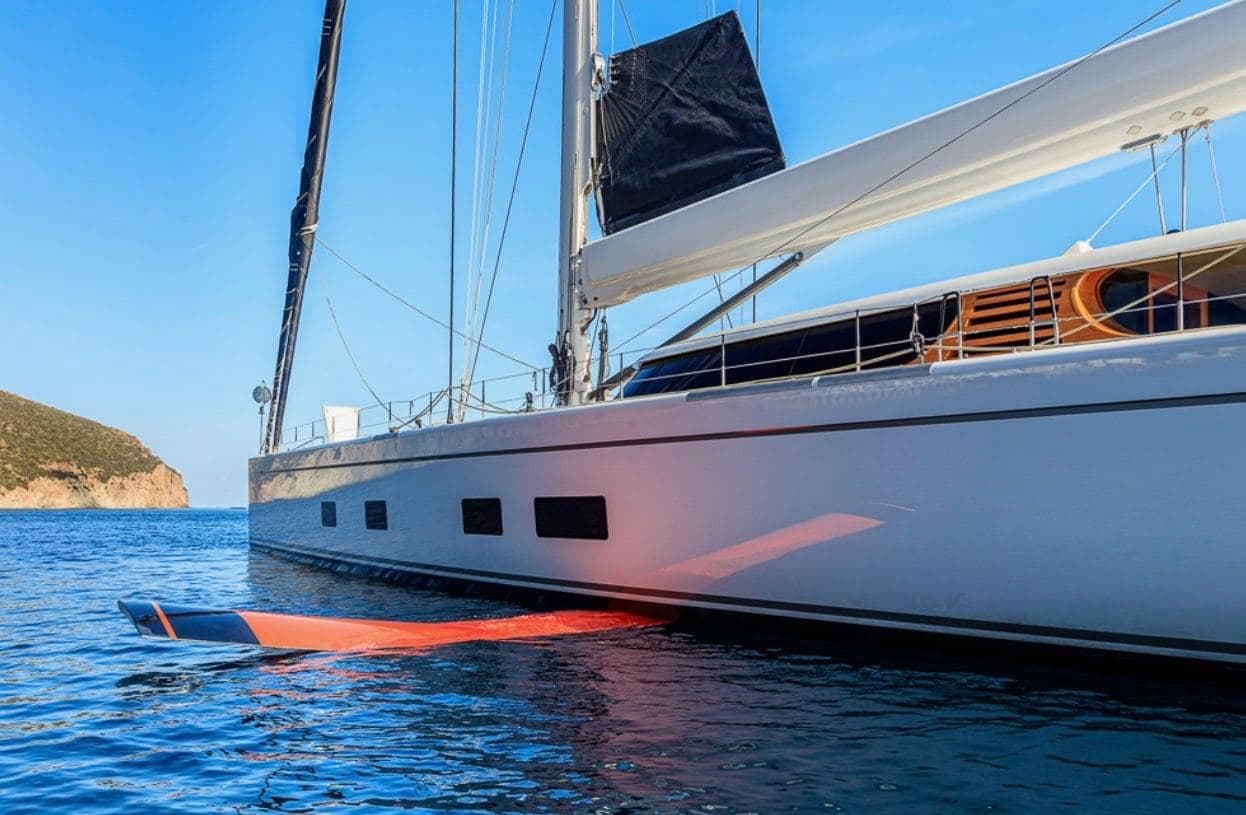
Interesting links:
Farr Yacht DesignAmerica's Cup Aerodynamics - Interview with AIRBUS - Part 1
America's Cup Aerodynamics - Interview with AIRBUS - Part 1
Run Your Own Simulation