Introduction
At Wingtra, we develop autonomous surveying drones which are used for surveying, mining, agriculture, environmental monitoring and many more use cases. I am working in a 50/50 split between being lead-engineer and leading the Mechanics & Aerodynamics Team - being responsible for research and new developments.
Aerodynamic performance
Our drone is a fixed-wing VTOL drone. That means it can take off and land vertically using the vertical lift of the propellers. But for forward flight, it will transition into horizontal mode, allowing the fixed wing to generate lift. In that scenario, the propellers no longer provide lift but mostly the thrust required to overcome aerodynamic drag. This makes it much more efficient compared to a conventional drone which constantly uses the propellers’ lift to keep it in the air.
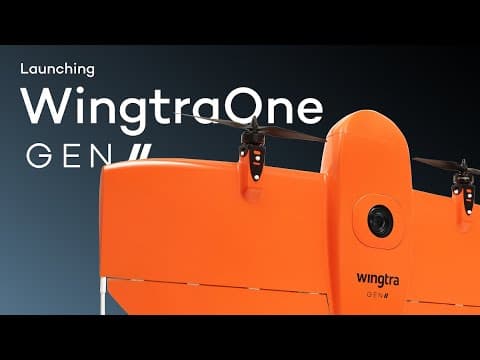
At the beginning of a new project or iteration, we have a lot of variables to take into account: payload capacity (the weight a drone can carry, mostly camera equipment in our case), cost, support points for the vertical landing & take off, cruise speed, wingspan and so on.
That means we are looking at a lot of possible variations and it isn’t easy to determine a clearly preferred concept. In the definition phase of product development we weigh certain features or properties and then go through a score-card approach. Through the use of simulations, we see which one comes closest in terms of aerodynamic performance and flight behavior.
Aerodynamic Design Tools
Several years ago, we had given the use of 3D CFD (computational fluid dynamics) tools a chance. When we later went to the wind tunnel for testing and verification, the correlation wasn’t very good. We kept an eye on the evolution in terms of CFD software, but until fairly recently, restricted ourselves to the use of fast but rudimentary tools like XFLR5 for the bulk of the initial conceptual work. Recently, we decided to re-evaluate CFD and work with AirShaper.
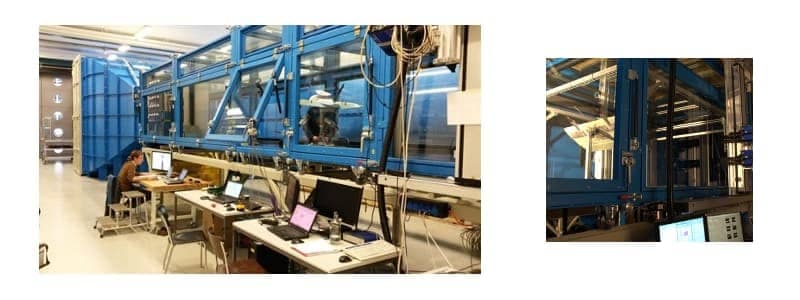
Concept exploration
With strong goals in terms of both lifting capacity (requiring high absolute lift values) and lift-over-drag ratio (the aerodynamic efficiency: maximize lift and minimize aerodynamic drag) and many other requirements usually given by the product team the concept phase is featuring difficult trade-offs. A larger wingspan means more lift capacity and a higher efficiency, but also higher bending loads and difficulties in transportation. For this explorational concept phase the ease of a browser based simulation is great.
It is a very beautiful balancing act where we try to combine the function of different elements, like optimizing the wing tips for both aerodynamic performance and compactness for transportability.
It's only by running high numbers of simulations that you really start to see trends and find areas for improvement. In the past, this meant spending hours setting up a simulation, as it involved cleaning the CAD geometry (to make it watertight), creating the mesh (and manually improving it), processing the results into visuals and so on. With AirShaper, the process is automated, so we could simply launch dozens of design concepts at the same time in a matter of minutes and look at the results just hours later.
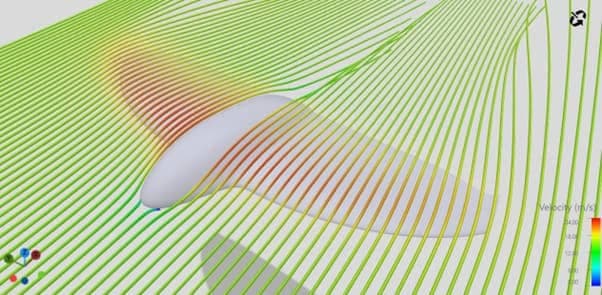
Flight testing
Design tools are highly useful, but in the end, the real drone flying through real air is still the ultimate test. So we literally have a dedicated team of multiple people flying the drones day & night to validate their performance, UX, reliability and many other factors out there in the field. We call the team the continuous testing (CT) team.
Wind tunnel testing
One downside of flight testing though, is the limited control over the conditions and limited measurement data. In a wind tunnel, it’s much easier to position the drone at fixed angles of attack, vary the speed and other parameters in a very controlled way. At the same time, by mounting the drone on a measuring balance, we get highly precise insights into the lift & drag forces and the pitch, roll and yaw moments on the drone. This allows us to precisely map the aerodynamic properties of the drone, which are then used as input for our autonomous flight controller.
The major aspect of wind tunnel testing is that it allows you to verify your simulations. After all, the better the correlation the more you can rely on simulations for further design work. To do so, we had to consider and calculate air densities, blockage factors and compensate for the influence of the mounting structure (the parts connecting the drone to the balance also generate drag & lift!).
Once we had done this, we were truly satisfied to see a very good correlation between the wind tunnel data and the CFD simulations:
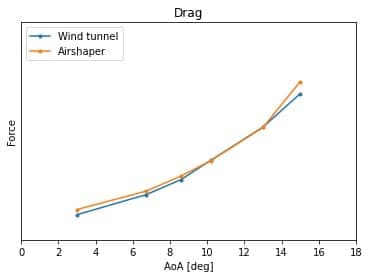
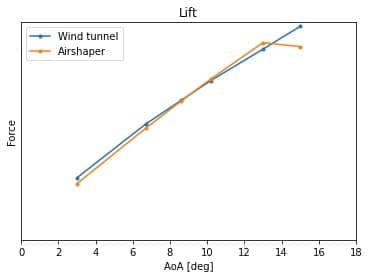
Neither wind tunnel nor CFD are perfect: prototypes can (and will) have non-perfect surface finishing and there are balance measurements errors. Similarly simulations have uncertainty with modeling, discretization and iteration errors. But when both are performed correctly, they both feature a small error band and the correlation between them becomes apparent as visible in the graphs.
Further work
Seeing this correlation, we have great confidence the drone will perform as projected. CFD has become an important part in our toolbox and we’ll use it with confidence for this and future projects. As the computing power & functionalities of CFD increase, we’ll surf the wave and benefit from it. It will not replace wind tunnel testing or flight testing all together but for sure its relative importance will grow and will help us to speed up developments. At our peak, we run over 100 simulations per person per month!