The challenge
Climate change is slowly moving to the top of the agenda for most businesses and governments, with countless regulations and incentives now in place to reduce our impact on the planet. One sector that is making the most substantial changes is transport, with cars seemingly the main focus in the media. However, there is small mention of the efforts to improve the sustainability of truck, buses and coaches which make up around 27% of all road transport emissions in Europe. Therefore, reducing the emissions of this large group of vehicles through aerodynamic optimization and improved fuel efficiency could be the key to helping the transport sector in its mission to combat climate change.
How the Vecto AirDrag tool can help cut truck and bus emissions
The status
For decades trucks have been designed to move cargo as efficiently as possible within a regulated design space, resulting in large box shapes that maximise the cargo area. However, these box shapes are not aerodynamically efficient which is why the drag coefficients of trucks range from 0.7 to 0.9. That’s significantly higher than most production cars, with some of the latest models such as the Tesla Model S achieving drag coefficients as low as 0.2.
Futuristic designs
With future regulation changes in the dimensions of trucks, increased packaging freedom and the reduced cooling needs of electric drivetrains, engineers now have much more freedom to try and minimise drag. For example, the Tesla Semi features a smooth transition from the truck to the trailer as well as covered wheels which help achieve a drag coefficient of just 0.35. Taking aerodynamic optimization a step further, the Betterflow Future Truck improved the underfloor aerodynamics to feed fresh air into the wake, further reducing drag. Initial Computational Fluid Dynamics (CFD) simulations suggest that the resulting drag coefficient of the Betterflow Future Truck is approximately 30% lower than the Tesla Semi.
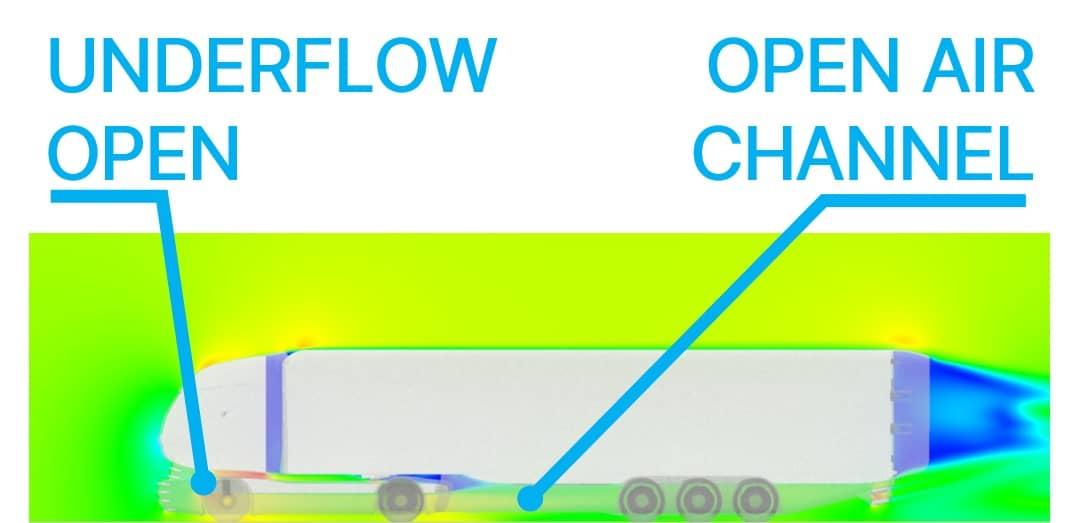
Realistic changes today
However, the Tesla Semi is not yet in production and the Betterflow concept is even further away from driving on our roads. Therefore, to reduce emissions now we need to optimize the aerodynamics and improve fuel consumption of existing fleets. This is precisely what manufacturers like Wabco and Transtex are doing. By integrating features such as side wings and modifying the tail of the trailer to close the wake, manufacturers claim they can achieve over 10% fuel savings.
How the Edge Elite Aero System achieves 10% fuel savings
Further improvements
In most cases reducing the wake behind a trailer involves geometries that provide an “inward” momentum to the air so that it fills the wake. One method of doing this involves adding a tail to the end of the trailer. If done properly, this tail will guide air inwards and remain attached.
When the regulations don’t allow for such extensions, another technique is to add a small bump ahead of the trailing edge of the trailer. This pushes the air outwards initially and as the flow makes its way back inwards, it builds up “inward momentum” by the time it hits the end of the trailer. Such features are very sensitive to small changes in geometry. If the angle is too shallow it has a limited effect, whereas if the inward angle is too high, the flow could separate.
Automated optimization
AirShaper's Aerodynamic Shape Optimization is a vital tool for creating geometries that result in maximum aerodynamic performance. The example below shows how the algorithm is optimizing the shape of the end of the trailer, with the results similar to what is currently being used today, such as the bump ahead of the trailing edge. A fascinating aspect of the software is that no previous information about such concepts was inputted into the algorithm, yet it still produced the same features.
This proves that optimization software can really inspire designers and engineers to create new and innovate shapes - which is going to be essential for developing trucks with less drag, lower fuel consumption and reduced emissions.