AirShaper’s new Aerodynamic Shape Optimization software
Did you know that professional cyclists spend over 80% of their energy pushing through air? While over 50% of the energy from fuel or batteries in vehicles is used to overcome air resistance at highway speeds?
Optimizing aerodynamics can be the key to unlocking performance, improving efficiency and reducing waste & greenhouse gas emissions. As we move towards a more sustainable future, industries are recognizing the important role aerodynamics can play in achieving energy efficiency. But how can this be done quickly, easily and in a cost-effective way?
AirShaper have developed a brand new Aerodynamic Shape Optimization tool which revolutionizes the conventional approach to aerodynamic design. Innovative algorithms automatically optimize a design's shape; helping you achieve aerodynamic performance targets and reach the optimum solution faster.
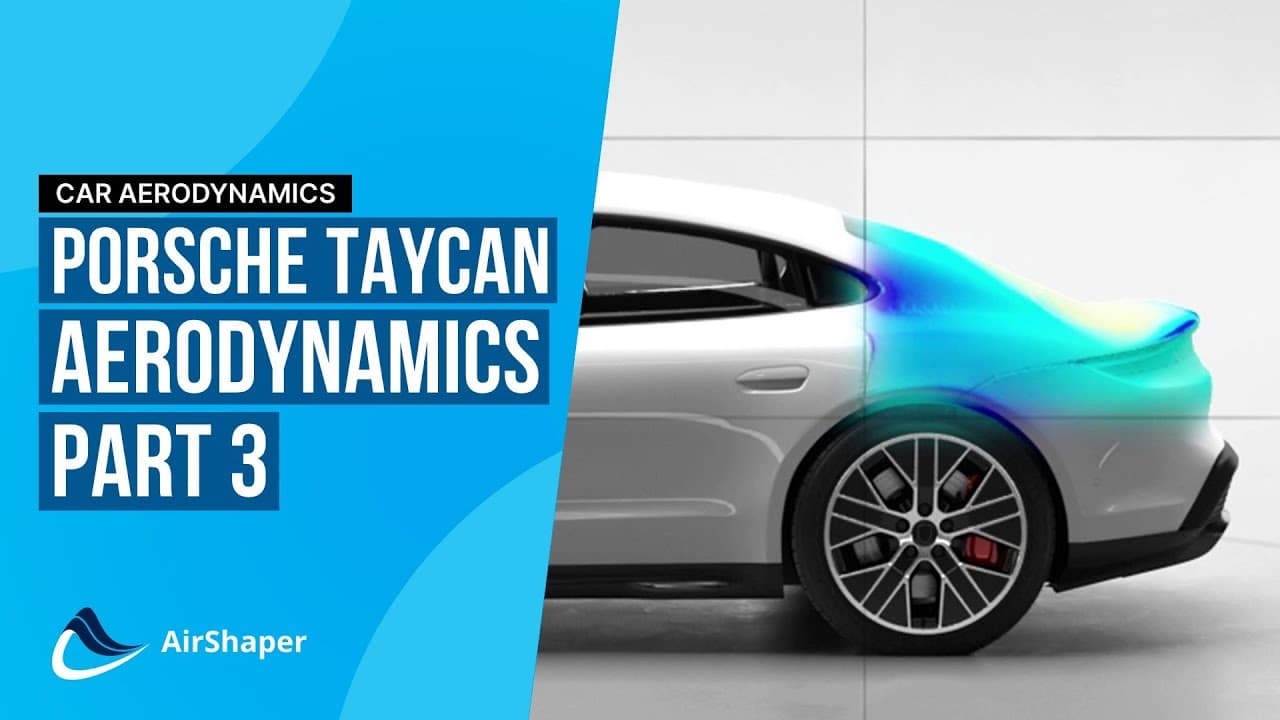
Aerodynamic Shape Optimization - Launch trailer*
‘Our mission at AirShaper is to make aerodynamic simulations accessible to everyone regardless of the industry you work in,’ says Wouter Remmerie, CEO at AirShaper. ‘This type of optimization software is usually only available within expensive software packages and normally requires skilled engineers to set up. But our new solution offers a quick, easy alternative that still achieves accurate and reliable results.’
Revolutionizing the conventional approach
Improving aerodynamic performance requires a detailed and iterative approach which usually involves CFD simulations and wind tunnel tests. Typically, CFD is used to analyse the initial performance of an object which engineers then use to manually tweak its design. These changes need to be re-evaluated with further CFD simulations or wind tunnel tests to quantify the improvements and the process repeats.
Over the last decade, CFD has become the tool of choice amongst engineers. Substantial improvements in computing power have meant faster run-times and more complex modelling techniques. Allowing engineers to replicate more realistic flow conditions along with finer meshes.
However, this aerodynamic development cycle still requires substantial budgets and long development times. Problems which shape optimization algorithms can help to solve.
How does Aerodynamic Shape Optimization work?
There has been a huge surge of development in shape optimization algorithms over recent years, making them now more reliable than ever.
Utilizing the adjoint optimization technique, these algorithms create accurate sensitivity maps of an object’s surface in just two simulations - instead of the thousands usually required. These sensitivity maps are then used to automatically morph the shape of an object which is then re-evaluated and the process starts again. This optimization cycle automatically repeats until the shape of the object has been transformed to meet its performance targets.
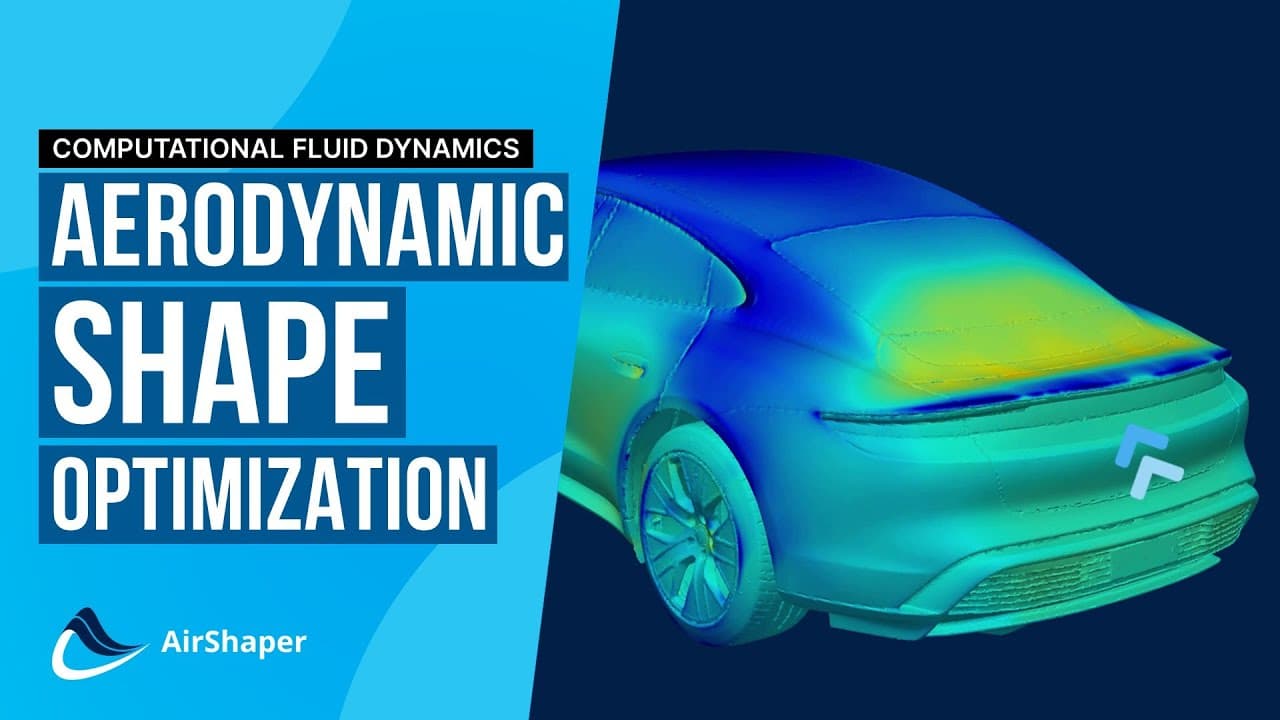
Aerodynamic Shape Optimization - How it works*
This automated optimization sequence means that users no longer have to manually adjust the shape of an object and re-run simulations. All you need to do is upload a 3D model, specify the orientation, wind speed, morphing space and optimization goal and the algorithms will deliver a fully optimized 3D model!
The benefits
The beauty of this technique is that it can be applied to any application where drag or lift are relevant.
Electric vehicles
Several electric vehicle projects have utilized this shape optimization approach to reduce drag by 7%. The less drag an electric vehicle experiences, the less energy it requires and the further it can travel on one charge.
Motorbikes
Companies such as MV Agusta have used our tool to increase top speed and downforce of their motorbikes. Improving handling both on the road and on track.
Sports
Our Aerodynamic Shape Optimization tool has also been used for Decathlon, a major sports equipment manufacturer, to optimize the performance of their upcoming Van Rysel bicycle helmet. Taking into account comfort, safety and ventilation constraints, the helmet was optimized to reduce aerodynamic drag as much as possible. Saving even just a tenth of a Newton in drag force can lead to seconds of difference on a time trial.
Aviation
As the aviation sector pushes to reduce carbon emissions, maximizing the efficiency of fuel or batteries is crucial. Shape optimization can be used to generate more lift for a higher payload capacity or to design for higher efficiency to extend range.
Renewable energy
Shape optimization has also been used to reduce wind loads on renewable energy equipment, such as solar panels and offshore structures. Improving the lift & drag forces and moments of these devices is key to guarantee safety, operability and efficiency.
Start-up companies
AirShaper’s optimization platform allows small companies to make fast gains in aerodynamic performance without having to invest in complex software packages or trained engineers.
To streamline your aerodynamic optimization process, whatever industry you are in, get in touch to sign up for AirShaper’s new Aerodynamic Optimization software
*The optimization shown in these animations is an independent study based on a 3D scan provided by A2MAC1 and is not endorsed by any OEM.