INTRODUCTION
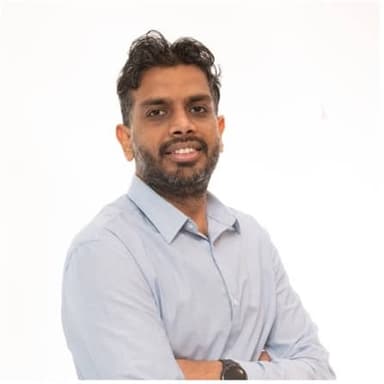
From the fastest foils of America’s Cup boats to innovative electric hydrofoiling vehicles, Nitin Garg has been working on the most advanced foil designs. In this interview, he shares with us fascinating insights on hydrofoils and how this technology is shaping the sailing world and maritime industry.
Livia: Talk me through your career path and how you got into this industry.
Nitin: My professional journey started in India, where I did my bachelor’s in Marine Engineering from Tolani Maritime Institute, Pune. The course mainly focused on the various systems and engines you find on ships, and how you maintain the engine room on a merchant vessel for example. It was when I took a Naval Architecture course during my third year, taught by a professor coming from University of Michigan (UMich), that I became passionate about this area. While it was not a core subject, I got really intrigued by it and from that point, I knew I wanted to study Naval Architecture. Before landing at University of Michigan to pursue a Masters on this subject, I worked at Shell and Seaarland Ship Management as a marine engineer for a period of four years. During that time, I learned a lot about working in a multicultural environment and responsibility: at certain times, you would be responsible for an entire engine room on a 300-meter ship. When I had saved enough money, my intention was to go to Michigan, study Naval Architecture and then come back to Shell. At UMich, I had the chance to work on several cool projects such as designing wind turbines in Great Lakes, and I ended up doing a PhD on high fidelity hydro structural optimization of lifting surfaces on hydrofoils. It was very CFD-based, and the learning curve was steep as I had to learn a lot of coding and numerical methods, but I eventually enjoyed it a lot. In particular, I appreciated the experimental side of it: we could actually build the optimized hydrofoil and test it in a cavitation tunnel in Australia, where we also had the baseline foil, so we could do back-to-back comparison. After that, I went to Imperial College London where I went from studying external hydrodynamics to internal aerodynamics, working on optimizing turbocharger for off-road vehicles. I then started working at INEOS Britannia in the UK. My PhD topic was very similar to what was happening in America’s cup at the time. I was initially developing UI software for foil design, next I moved to fluid structure interaction where I was part of the foil design team, and eventually I moved on to performance data analysis towards the last phase of the previous America’s cup.
THE AERODYNAMICS
Livia: To start off, what is a hydrofoil and how does it work? How are boats capable of “flying” on water?
Nitin: A hydrofoil works just like an aircraft wing: you have a cambered surface, where differences in pressure are present between the top and bottom surfaces; because of this pressure delta, a force is produced in an upward direction.
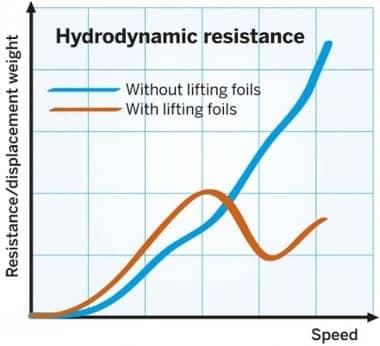
As you start getting faster and faster, your wing will start producing lift (as the lift force is directly proportional to the square of the velocity) and you take off. Similarly on boats, because the hull has buoyancy, you can float on the surface of water. When you have enough speed and you put those similar looking aircraft-wings under the hull, the boat “takes off”, and slowly the weight of the boat is entirely on the foils. Because the hull has a much bigger wetted surface, it causes a lot of drag when navigating, while foils are small surfaces that produce a lot more lift. Basically, the lift-to-drag ratio (or, efficiency) of the foils is more than double the hull in most circumstances, except at very low speeds. The hydrofoils are highly beneficial as you can go faster and farther with the same energy (which can be provided either by conventional fuel or battery). Using hydrofoils, we can reduce the drag of the craft by up to 90%.
Livia: Hydrofoils come in different shapes and belong to two main categories: surface-piercing and fully submerged. What are the advantages/disadvantages of different configurations? How differently do they perform?
Nitin: Hydrofoils are just like aircraft wings; we want to have an aspect ratio value as high as possible. However, in water we have to deal with a much higher density (1000 times) than in air, resulting in much higher structural loads. So, for example, it is not possible to just have a massive cantilever beam like for an aircraft wing. This is why the span has to be managed in the case of hydrofoils.
Surface-piercing foils are the concept we see in AC75, the America’s Cup craft: with these foils, when you are going at high speeds, lesser wing area is required to produce the same lift, i.e., the weight of the boat, compared to at lower speeds. Thus, there is a possibility to reduce the wing surface in water and gaining more efficiency by piercing. And as the wing pierces more out of the water, it results in valuable drag savings. The lift requirement stays the same as weight stays the same; as speed increases, lift increases by the second power of velocity, so you need less wing surface to generate lift, which is automatically done as it lifts out of the water. As you slow down, you sink again, having more wetted foil area, so it is self-balancing as well. And when looking for performance advantage, this is what can make a difference.
However, one of the disadvantages of this configuration is ventilation, and it is extremely important to take it into account during a design phase. Ventilation is the phenomenon occurring at the air-water interface of the hydrofoil piercing the water when air gets sucked down the lifting surface of the foils and therefore lift is compromised, and the hull falls back on the water. At the moment we are relying on some empirical methods and real-world testing to predict and better understand the ventilation behavior. CFD is a work in progress, as it is quite difficult and computationally expensive to simulate this effect of air and water together. It has been done but it is not as simple as simulating pure water or air.
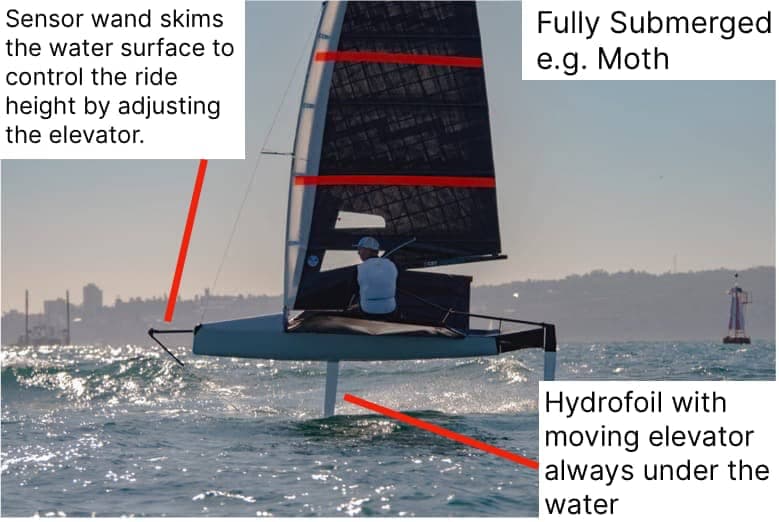
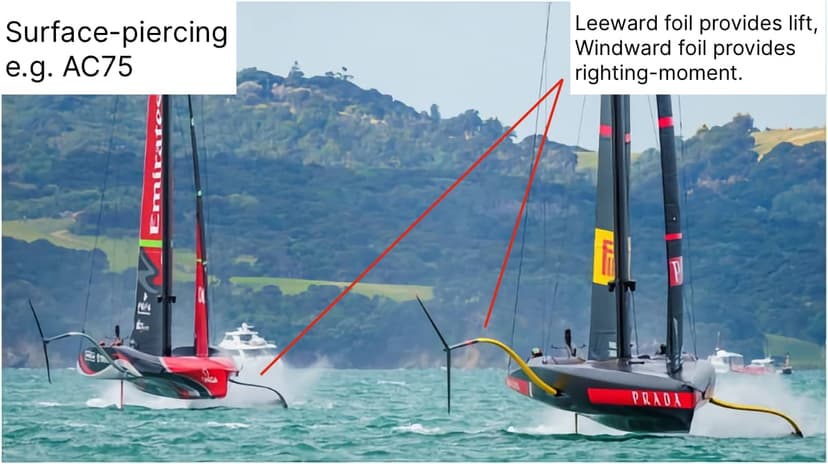
On the other hand, many hydrofoils are designed so that entire foil stays below the water line. It is the easiest and conservative option to have a safer ride for the user and it increases the wave handling capacity. In most of the commercial crafts, including Candela boats, the idea is to have the foil always underneath the water because it is a safer and more reliable system. This type of boats is also expected to go to different places and sustain different conditions, and you don’t have America’s Cup sailors tuning the ride height accordingly to the waves. With submerged foils, as you speed up, the lift would keep on increasing. To have constant lift (once you have enough) you need to reduce it by reducing the "angle of attack" of the hydrofoil; and this requires an automated system, so that occasional (non-professional) "drivers" can also enjoy the boat. In this case all you need is a good flight control system, and you’ll have a safe ride, different from sailing with surface-piercing foils where, in the event of your entire foil getting out of the water, that hull might crash on the water, a “catastrophic event” in racing. It is also dangerous in case there are people or objects around in the same area if you have a piece of metal out of the water.
The downside of the fully submerged foils is that this entire foil stays wetted, generating more drag compared to a partially submerged one. However, in the case of commercial crafts, performance is not the only parameter. Additionally, power is less of an issue as you are often putting a motor on the boat, so drag is slightly less important.
THE DESIGN PROCESS: AMERICA’S CUP HYDROFOILS
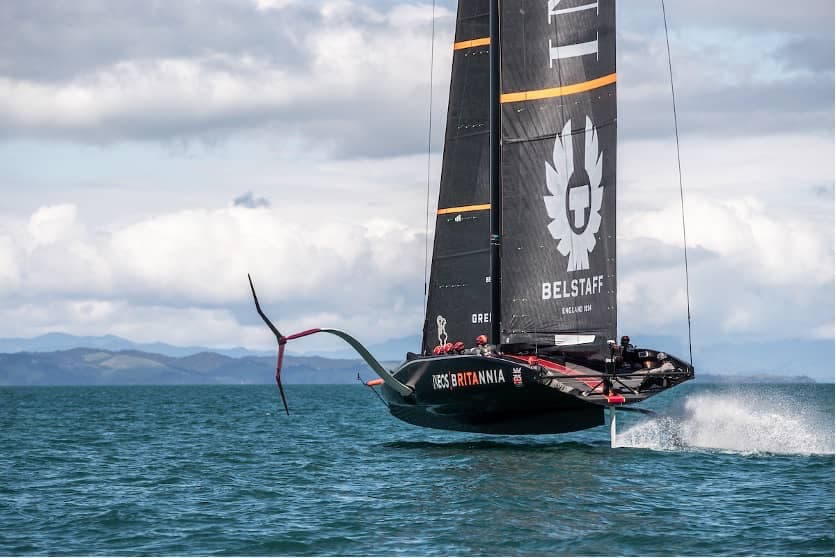
Livia: The most “famous” hydrofoils are the ones from the America’s cup boats. From your years at INEOS, could you talk about how the team develops the hydrofoil design? Besides race regulations constraints on the overall sailboat, a wide design environment is left for exploration when it comes to designing the foils. What approach do the engineers follow?
Nitin: I’ll discuss the methods we used in the last campaign (36th America’s Cup), the one with a new set of rules, new class of boats, the first-time involving foiling monohulls.
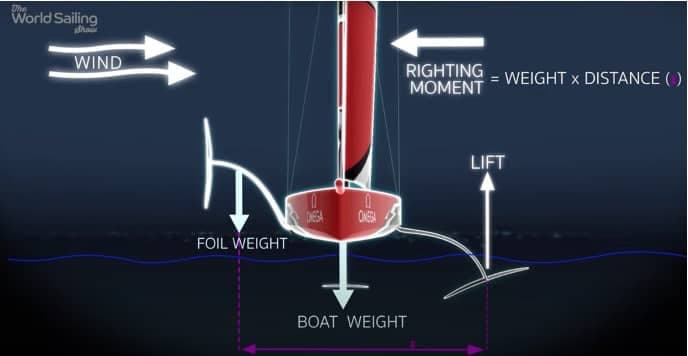
To start with, we had to completely understand the force balance on a monohull, you need to consider the forces from sails and foils and the moment each of them is generating for the boat to be balanced. Of course, this was done using a low-fidelity tool because there is a big design space to explore. When we started last campaign the design space was huge, there were so many different design decisions to make, each with its pros and cons. For the low-fidelity methods, while some teams were using lifting line, others were using vortex lattice methods. It doesn’t matter which tool you use but it should be fast enough and accurate enough to look at thousands of designs…we were just going wild at a point. After the initial design space exploration, almost half of those designs would come out to not be feasible for regulations. In fact, all boats for America’s Cup racing need to follow very specific rules. For example, the foil designs had to fit in a specific rectangular box and be symmetrical about a given axis, while there is a weight limit to be met and a limit for the center of gravity (CoG). Next step was improving the models, optimizing for CoG and weight, as well as conducting separate optimizations of the wing using CFD to increase the fidelity or through RANS-based correction surfaces to account for the junction in the center of the foil for example. Then we ran optimizations for the entire sailboat optimizing for VMG (Velocity Made Good), sometimes in a static environment, where all accelerations were constrained to zero.
Livia: Is there a simulation that takes into consideration the aerodynamics of the sails as well as the foils? How are computational methods carried out?
Nitin: Sails are just as important as the hull and foils. There might be a foil that does not work well with a particular sail for example. I think having a computational system where the sails also have a lifting line or a vortex lattice method to optimize the sail’s deformed shape is what the teams are currently trying to achieve. Although if one wants to capture a ground effect, that is not very well represented by low-fidelity tools. One way to solve this problem is by using a response surface for the physics you cannot model; this allows to reduce computational time for design studies. For example, the next race will take place in Barcelona, where the sea state is quite different from Auckland, where the last America’s Cup happened. In the Spanish sea, there are more waves to account for, and low fidelity methods are not particularly great in capturing the free-surface effects. So, a robust CFD model done beforehand to see the effect of waves on the hull is important to train valid response surfaces.
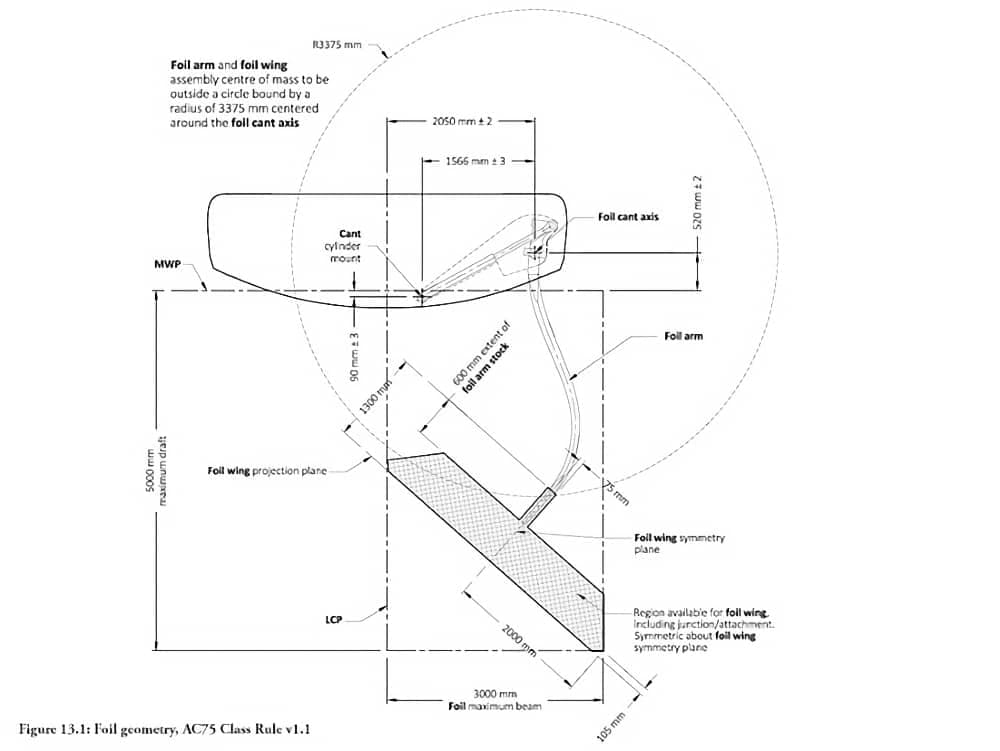
Livia: How are design tools validated?
Nitin: The use of the towing tanks, or, the cavitation tunnel are banned under the current AC rules. Thus, test boat becomes a critical component to validate the models. Thus, before the final race boat design, most of the teams design a test boat with focus on mainly the things they really want to test and confirm the behavior, for example, ventilation. There is a lot of effort currently being spent by the America’s cup teams to improve their tools both in terms of accuracy and speed. Thus, the idea is not to make the fastest test boat, rather a boat from which the team can learn from and then improve and validate the tools.
Livia: How important is working alongside sailors during the design phases?
Nitin: For us engineers, when we see a number, we take it on its face value. We usually do not have a feeling of it, whereas the sailors have a deeper understanding of the practical limitations of a boat, especially in a race environment. Thus, the sailors knowledge is highly critical to design the constraints in the optimization process. I would say 90% of the time, when they have an intuition on something, that comes out to be right. Engineers take the sailors feedback very seriously, even though the majority of the sailors might not be engineers. The design group take sailors’ feedback as a feel and then they go back to dissect it using the data and work with sailors to improve it.
For example, when the designers are doing optimization and are trying to find minima, the sailors sometimes go “what if we are away from the optima slightly”, as they know it will most likely happen, especially in a racing situation. Designers use the sailors’ experience in real-world to look at a flatter optimum rather than a peaky optimum.
Interesting fact: I have never sailed in my life, so to be able to look at data and tell Olympic medal winning sailors “this or that” is something that they can improve on, feels weird at times. However, you also need to consider a particular way they want to sail the boat. For this reason, sailors are very present during the design phase, so that they know how the boat is designed, and can sail it while being aware of the design choices. Doing a lot of performance analysis towards the end of the campaign and working consistently alongside sailors was a very engaging experience for me.
Livia: How do you design foils accounting for waves?
Nitin: This is a very challenging problem! One way to handle this is that the designers put a constraint on the design. For example, if we had to sail in waves of 1-meter significant wave height, we would design the foil such that the junction of the foil, at that wave condition, should never pierce. Of course, you sacrifice the performance in flat water, so this is where the strategy comes in. Each team makes design decisions for conditions they would definitely want to win the race in, and you accept that outside those conditions, the boat’s performance will be slightly compromised. The designers spend a lot of time to minimize that drop-off in the performance away from those design conditions. A team can optimize intensively for one specific condition, but this often means you have poor performance in all other conditions.
Livia: Which road do the teams choose: optimizing performance in a specific condition or optimize a boat that works and performs well over a wider range of speeds and conditions?
Nitin: Normally, every team will have a different strategy. For example, in the last America’s cup, some teams had their boat’s peak performance at higher winds speeds, while the other teams had their boat more optimized for the lower wind speeds. Most of the time, the meteorology, performance and strategy group of each team will work together to define these conditions along with the sailors.
Additionally, when sailing at 45 knots, it is very difficult to sail the boat at its optimum. So, there is some consideration given to that as well: it is not worth optimizing for 45 knots to the last tenth of a knot as we probably cannot consistently sail at that condition optimally; this is where sailors’ feedback becomes critical.
The teams are also looking at the weather, sea state for the location we are going to race in, during racing months. So, if the average wind speed in Barcelona is 7 knots, one would not want to design the boat for 14 knots. The teams should start giving up performance at higher speeds for better performance at lower speeds.
For this reason, what most teams are trying to achieve now is what we call “multi-point optimization”. The boat design which would win in Auckland, will probably not win in Barcelona due to the significantly different environmental conditions. I think Barcelona will be a very challenging place to sail in, with a lot of water coming from the shore and a lot of waves and mixing going on. The wind speed there is also slightly lower and for this reason, the rules have been changed accordingly so that these boats work better at lower wind speeds (the aspect ratio, the width of the design box has increased to have more efficient foils).
Now every team has a better understanding of the design direction as per Auckland, but now stability and control will become more important because sea state and average wind speed is probably going to be significantly different in Barcelona.
Livia: What are the main challenges? One of them seems to be stability. How do you maintain the boat trimmed?
Nitin: It is important to note that it is very difficult to make an “autopilot” for these boats because as per the class rules, there has to be a certain delay (usually 1-2 seconds) as per the class rules. Control mostly lies in sailors’ skills. They control the control surfaces (no pun intended!), i.e., the foils, as well as the inclination of the elevator of the rudder to control pitch. Sailors are always “looking out” to control the boat and foils usually have some kind of markings to give the sailor a depth indication; or for example, one team also had cameras placed on the hull looking at foils, to control tip and junction position.
Livia: What about the cavitation effect?
Nitin: During the design phase, the designers are always talking about the cavitation bucket. For a given 2D hydrofoil section, there is a cavitation bucket which the designers would always try to play with: how can we make it deeper and wider. The most challenging thing is take off, where we want to produce a high coefficient of lift and in that case, you are worried about leading edge cavitation and stall. At high speeds, you need to consider trailing edge cavitation instead. These effects are to be avoided or managed and are always considered when designing the foils.
Livia: Does take off speed always have to be minimized?
Nitin: Not necessarily!! During the last campaign, ETNZ had the smallest hydrofoils (at least as per my personal calculation) of the fleet, so they naturally had a relatively higher take off speed. Nonetheless, their approach was to have a boat designed to accelerate faster to take off, and then would have a lesser drag once the boat is completely on hydrofoils. Some teams put more effort on the take-off performance, other teams put more weighting on the high-speed performance. That is the reason we see different boat and hydrofoil designs in the last America’s cup. And that is why, even if everyone is designing for the same sailing conditions, teams come up with different designs. Some teams had the same performance tools as well. Still, they ended up with very different designs.
There is a lot of strategy, data analysis and intuitive call involved in making that decision. Once again, the sailors’ feedback here is critical, so they should be onboard for the conditions the designers are designing the boat for.
FROM RACING TO OFFSHORE AND PRODUCTION BOATING
Livia: Since the America’s Cup, hydrofoils are becoming more and more popular in a lot of watersports. The trend is clear.
Nitin: I think we are living in the exciting times, looking at the luxury personal yacht market projects like Candela or at more transport-based products like Boundary Layer Technologies and Artemis technologies. For commercial crafts, hydrofoils are becoming a common reality: in the short to medium term, I believe a lot of enthusiasts will want to explore the new technology. Considering the way this technology will accelerate within 10 years, I think eventually if we can make the foiling system safe enough, it is definitely a possibility to see a lot of foilers around, it will likely be a thing that most of the boats will have in some capacity, either hydrofoil-supported or fully hydrofoil flying craft.
One of the challenges, however, is the maintenance. Take for example, the maintenance associated with the aircraft wings. You cannot have foils under water round the year, it will have a significant damage on the control surfaces. But of course, we can come up with foil-design that the user can remove from the boat when in port.
Regarding offshore sailing, there are already some hydrofoils supported boats, where the foil is not meant to be only load carrying element but is supporting the boat. However, waves in offshore sailing have a big impact and, in my opinion, it will be a challenge but eventually achievable, with a good retraction and control system.
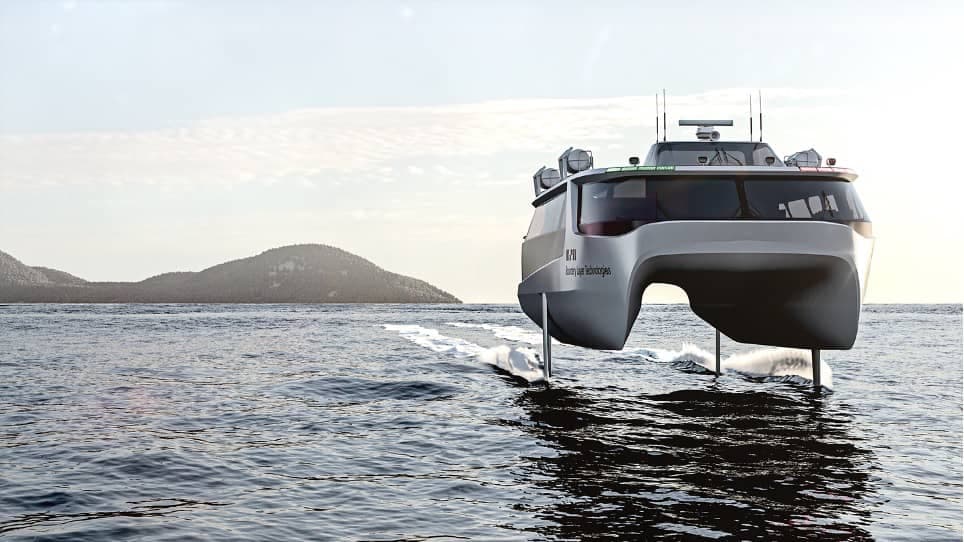
Livia: I have seen you are working with the team at Boundary Layer Technologies, a startup with the goal to make zero-emissions passenger and cargo ferries using hydrofoils. Tell me about the project.
Nitin: Yes, correct. There are high ambitions at BLT, and what we have realized is that it is important to take small steps, rather than going straight to a big ferry or cargo ship. So, we have started to join the jet ski market first and came up with VALO Hyperfoil, where we can prove out our hydrofoil technology, get enough funds in the company, and then move on to the bigger scale projects. Essentially the foil technology system is the same: once well proved, it can be transferred to the bigger crafts projects “just” at a different scale.
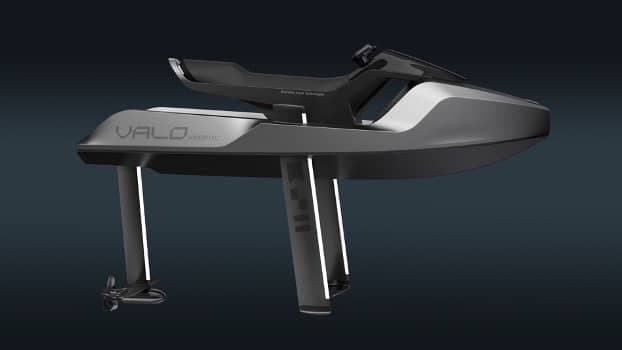
Livia: Can hydrofoil technology help toward electrification of passenger ferries or cargo ships?
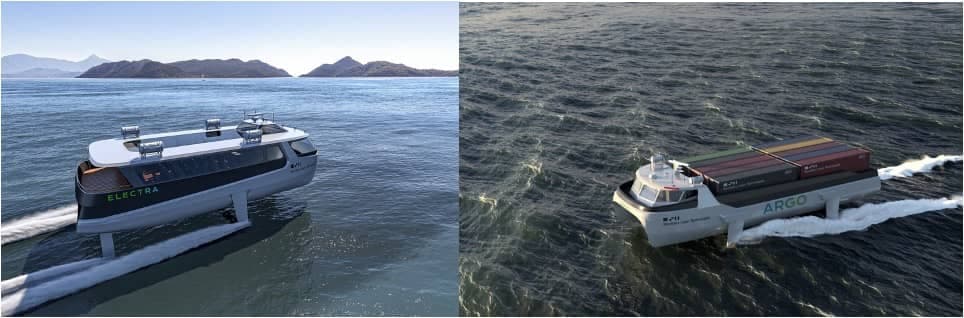
Nitin: It is interesting that there is a lot of demand for the hydrofoil technology these days. While it started out as something cool and fast in the America’s cup, now the maritime/transportation industry is looking at hydrofoils as one of the options that can help it go faster towards net zero goals. On normal merchant vessels, full electrification right now is not an option, because of the massive power requirements. And because of the recent increase in the sales of electric cars, electrification infrastructure is also developing at a rapid pace. Therefore, everything is going in this direction, and we should probably have more electric boats as compared to a motorboat.
Livia: What are challenges for hydrofoil combined with electric propulsion? Do you place the propeller upstream or downstream of the foil?
Nitin: It can be both ways. Obviously, the propeller efficiency slightly reduces if you are putting it downstream. The way we made that call for VALO is with the logic that as wings are primary lift producing surfaces, we wanted to have the best possible flow on our foils resulting in having the propellers in the downstream. However, this is an important study, which we have not yet done properly, and will put effort for production scale to better understand what the actual losses between upstream and downstream positioning are. In terms of foil area, we don’t have any surplus area on the foils: once you have a required area and you put it in the downstream of the propeller, you’d need to increase the area of the foil. So, it is really a matter of understanding how much the foil efficiency versus the propeller efficiency is reducing due to being in the wake of other control surface.
Livia: In case of bad weather conditions, when foil boats are running on the hull, rather than their foils, they have a great deal of drag produced by the foils themselves. How is this addressed and how much it influences performance?
Nitin: The way to account for that is a retraction system. There are different ways. In America’s cup, you just cant out (rotate the foils out of the water), whereas in BLT VALO, there is a straight retraction system (the hull has slots to place the foils in). It is slightly more challenging for a boat with a propeller because you need to have some amount of strut in water, even in the “retracted” condition.
For the rudder, we are working on it. You can have multiple places you can lock the rudder and elevator in, in order to have only the minimal stress.
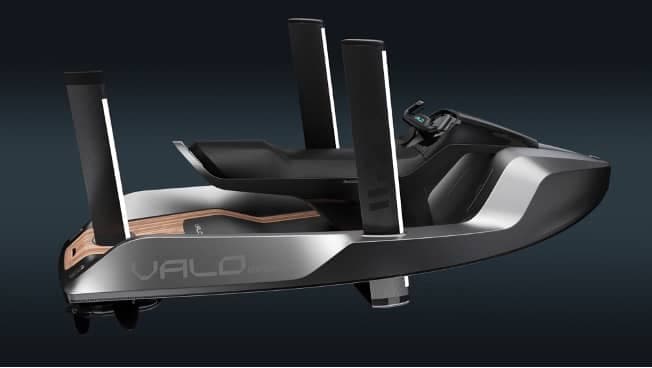
THE BOAT OF THE FUTURE
Livia: Will most crafts be flying on water with hydrofoils in the next 10 years? What are the future areas of focus and research?
Nitin: Right now, there is a lot of hydrofoil demand, and for this reason the technology will develop much faster, I think. Eventually, within 10-15 years, everyone (other than the sailing purists) will have some sort of foils on their boats. One of the biggest challenges now is getting a very stable control system to guarantee an overall safe and reliable sailing experience. Perhaps we will see advancement in autonomy, somehow figure out how these boats can foil “on their own”. Right now, sailors are controlling the boats, and if you put the control system replacing the sailors it will do a worse job, because sailors are intuitive, and they can see the waves which are coming in and they act accordingly. So, there is a need for autonomy and flight control systems to get better soon. Especially, if it is not a pleasure craft, but a cargo ship for example, you want an autonomous system. You cannot have just somebody who is playing with the foil angle the whole time. We will need some kind of prospective 3D view of the surroundings, like the one we see in the automotive industry with autonomous vehicles. A few start-ups are coming up, where they map the entire ocean around you in terms of waves, and then the control system can take that as feedback and will predict when there is a wave coming, and adjust the foil angle to achieve the desired level of depth in the water.
Livia: Will we be saying goodbye to classic hull sailing?
Nitin: I think sailing purists will still deviate and lean towards hull sailing. Although in racing, like in the Olympics, we are seeing more and more foils-based boats. Traditional sailing requires a lot of skill, whereas hydrofoil-supported boats with a decent control system should be a lot easier, and I believe it will open up the sea for a lot more people. And the next generation struggles with low speed; people are going on hovercrafts even if they are not using it for travel, but rather just to experience that kind of speed. High speeds are becoming slowly “normal”, and as the technology improves, we will go 40-45 knots whether it is an adventure sport boat or a personal watercraft to use for your normal commute. There will be an interesting balance.
Livia: What are your plans for the future?
Nitin: I recently started working with a company called REGENT, a startup based out of Rhode Island that is making seagliders with hydrofoils underneath. It is a fun concept as well, to combine the latest aircraft technology with hydrofoils. We already have a quarter-scale prototype which works, and we aim to have a full-scale prototype soon. In the next few years, sea gliders will become an exciting new way of regional transport, fast and green. It is not far away.
Interesting links:
Boundary Layer Technologies
America's Cup - Interview with AIRBUS - Video 1
America's Cup - Interview with AIRBUS - Video 2