Few road cars are capable of achieving top speeds above 250mph (402kph) - the realm of the hypercar. Cars like the multi-million-dollar Bugatti Chiron Super Sport 300+ or the McLaren Speedtail are a couple of examples. But what if you had a supercar and wanted to achieve this hypercar level of performance?
This was the goal of 7X Design, who converted a Lamborghini Huracan from a 600bhp, 200mph (320kph) production supercar into a 2000bhp, 300mph (480kph) coach-built Lamborghini Rayo hypercar.
21st century coachbuilding
Coachbuilding is the engineering art of taking a base vehicle chassis and making it into something unique. In the 1920s, companies like HJ Mulliner created one-off Rolls Royce bodies for their customers. More recently, Pininfarina developed the Ferrari Enzo-based P4/5, also known as the 'Glickenhaus', which generated more downforce and less drag than the original Enzo. This year, 7X Design took a Lamborghini Huracan and created the Lamborghini Rayo, which featured a bespoke carbon fibre body as well as extreme engine tuning.
The Lamborghini Rayo brief
The project was instigated by David Gomez, founder of 7X Design and the owner of a tuned Huracan. He approached Adriano Raeli Design to see what was possible. 'The brief was pretty straightforward,' reveals Adriano Raeli, Design Specialist at Adriano Raeli Design. 'We had to re-engineer the aerodynamics of a car with around triple its original horsepower to create a matching aero body that would allow it to achieve its best top speed.'
'There were some practical limitations as we wanted to maintain the original road-going capabilities of the car,' continues Raeli. 'For example, the McLaren Speedtail is a special vehicle with an elegant shape, but it is compromised on the road in terms of ramp angles and overall length. We wanted to avoid this. We also couldn't change the roof and wide windshield because they were part of the structure. The A-pillar in particular generated problematic drag-inducing vortices.'
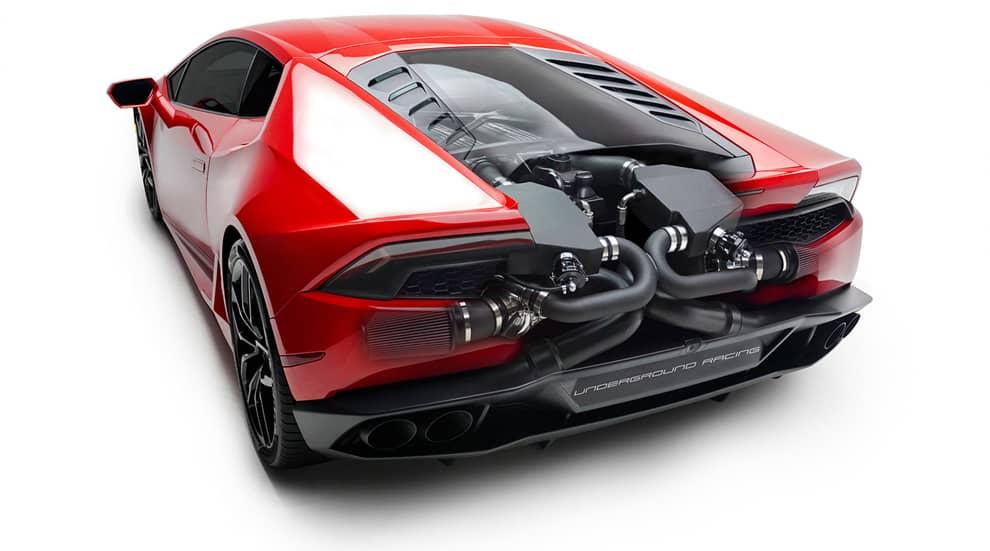
Inspiration to reality
Automotive styling is a unique mixture of engineering and design. The most elegant of lines often create unworkable aerodynamics. Despite the different aerodynamic requirements and Reynolds numbers, the project was specifically inspired by figher aircraft.
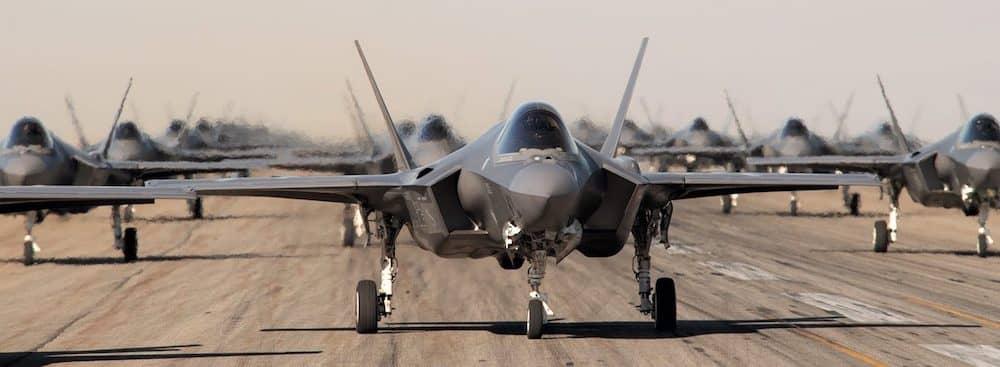
'They are one of the fastest and highly technological vehicles on the planet, short of spacecraft,' observes Raeli. 'When David saw the initial sketch he said, 'this is it!' That was the starting point of the design process. We then went from those quick couple of lines to a 3D model and then evolved the aerodynamic design of that model in simulation.'
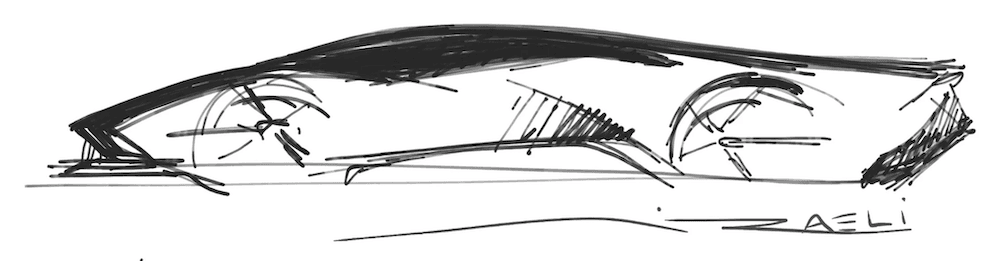
CFD simulation with AirShaper
There were three aerodynamic aims for the CFD programme:
-
Reduce the drag to allow the car to achieve the 300mph (480kph) target
-
Create balanced downforce to ensure the car remains stable at speed
-
Limit the total amount of downforce so the car doesn't get squashed at high speeds
To help achieve this, Raeli experimented with the design of the rear wing and in the end replaced it with two winglets. 'For some projects, a rear wing is a must, there's no other way to achieve that kind of downforce without a wing,' explains Raeli. 'To reduce drag, we opted for winglets instead, which are located in cleaner air. So I designed a general aerofoil profile and tested it in CFD. There was no specific math behind it initially, just general design and aerodynamic principles. AirShaper’s morphing tool was instrumental to evolving the design and it's helped us achieve better speeds and downforce without a rear wing.'
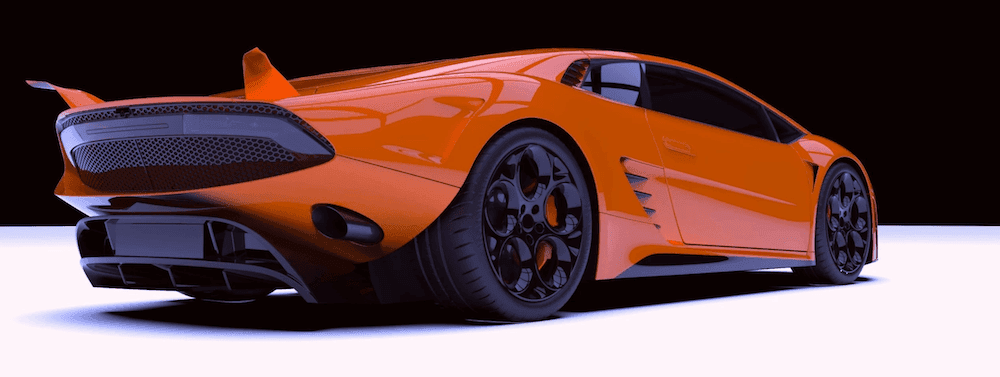
AirShaper's aerodynamic shape optimization tool also helped with the design of the underbody and the rear diffuser, which are essential as they generate significant downforce with minimal drag. The software showed that instead of a fairly square cross section, a more rounded and larger central tunnel with smaller side tunnels performed better.
A lot of effort went into the front splitter, to optimize the way the air is accelerated underneath the car. Additionally, large air curtains were added to shield the front wheels and reduce their drag. Other areas of improvement included the height and length of the tail, the rear window cover, side air intakes, front wheel well ventilation and more.
The benefits of CFD
AirShaper is not just designed for aerodynamicists, but also designers as well. The intuitive and easy to use software allows designers to make CFD a key element in their design process. 'You are able to test your design changes and see how they affect the aerodynamic performance of the car,' highlights Raeli. 'If we test a specific detail or a volume change in the nose for example, within a few simulations we can understand how it is affected, positively or negatively. We can then adjust the design for the next round of optimizations whilst keeping in mind the proportions we wanted to maintain.'
The results
Through the rounds of development, the drag coefficient was reduced by 28.5% to a Cd of just 0.279 whilst doubling the downforce (thanks to the optimized underfloor aerodynamics and top winglets).
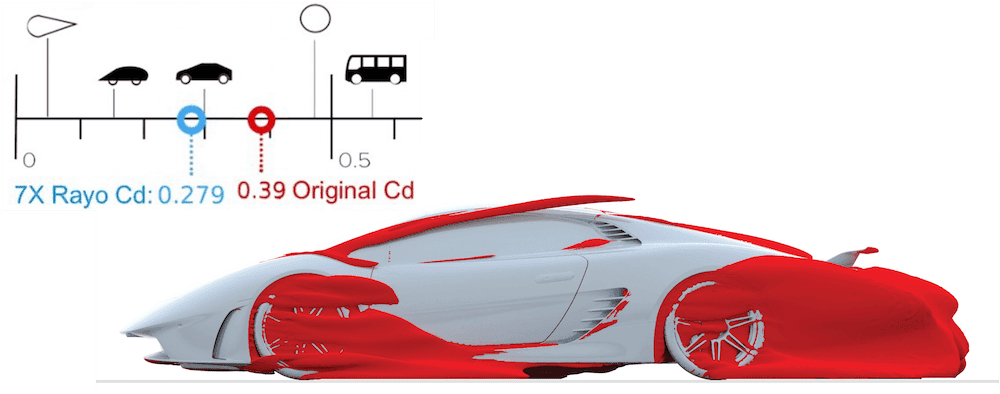
The car was taken to the IDIADA test track in Spain for initial testing of the new body, rendered in carbon fibre. The results were better than the team had hoped for, despite the limitations on the available straights. The car achieved 278mph (447kph) with more to come from further powertrain and aerodynamic development. Later this year, the car will be taken to a more suitable location to try to reach the 300mph (480kph) target.
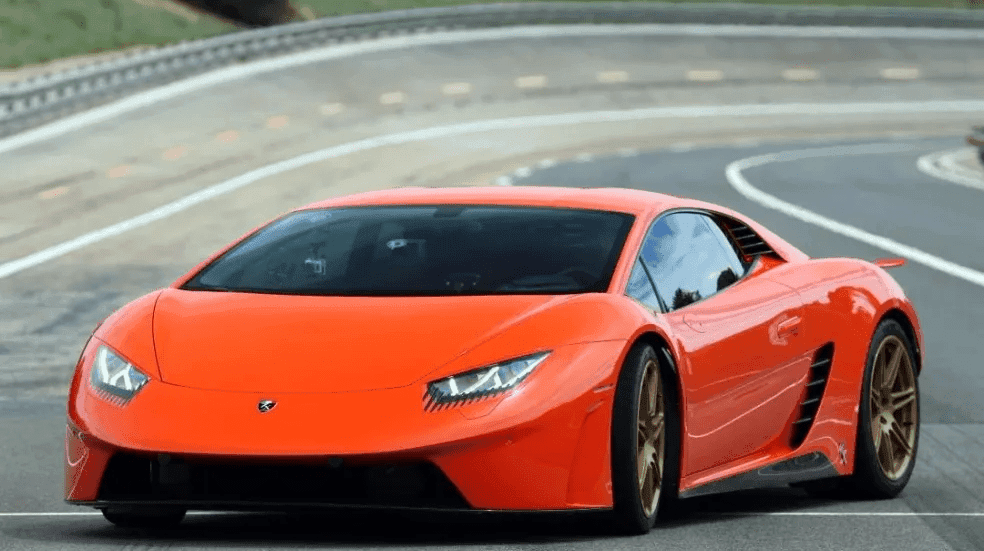
'What we have here is a great achievement because, if you think about it, how many companies attempt something like this?' questions Raeli. 'They usually have to invest millions of dollars in R&D and a lot of time. Whereas our small team, together with AirShaper's expertise and the knowledge of the people who built the car, allowed us to upgrade the Lamborghini Huracan to achieve those ambitious speeds. I think that's a pretty big accomplishment.'
Interesting links:
Check out 7x Design's Instagram
The IDIADA proving ground