Urban Air Mobility, or UAM, is the term given to a new form of personal urban transportation set to change the way we travel around our cities. It’s roots lie in the various flying car projects that have appeared over the last 70 years, but due to their impracticalities, have remained a novelty.
However, like many recent technological advances, the game-changer is the lithium-ion battery. The energy capacity and range of these modern day batteries could allow UAM vehicles to be certified to fly in our skies as early as 2024 [1].
The benefits urban air mobility can bring to cities
One of the main drivers for UAM is to reduce traffic, congestion and pollution in major cities, which is continuing to remain a problem. New York and London are two of the busiest cities in the world. Recent traffic surveys show that average car speeds were 7.1mph (11.4kmh) in central London [2] and 4.9mph (7.9kmh) in central Manhattan [3].
Contrast that to predictions that a UAM flight from Battersea to London Heathrow could take only 12 minutes. While travelling from Lower Manhattan to JFK could be a quick 8 minute flight. So you can start to appreciate the potential for urban air mobility and how it could revolutionise city travel.
eVTOL vehicles
The idea is for UAM to be part of a network of zero-carbon public transport that ultimately replaces cars on the road. The key to this is the development of Electric Vertical Take-Off and Landing (eVTOL) vehicles which combine horizontal and vertical flight using a mixture of propellors and wings. This allows eVTOL’s to take off and land vertically, avoiding the need for large runways, as well as horizontal flight.
As engineers continue to design and optimise this unique type of aircraft, new eVTOL concepts are coming to market every year. Although, all are based on the principle of transporting passengers across cities and landing and taking off on dedicated hubs known as vertiports.
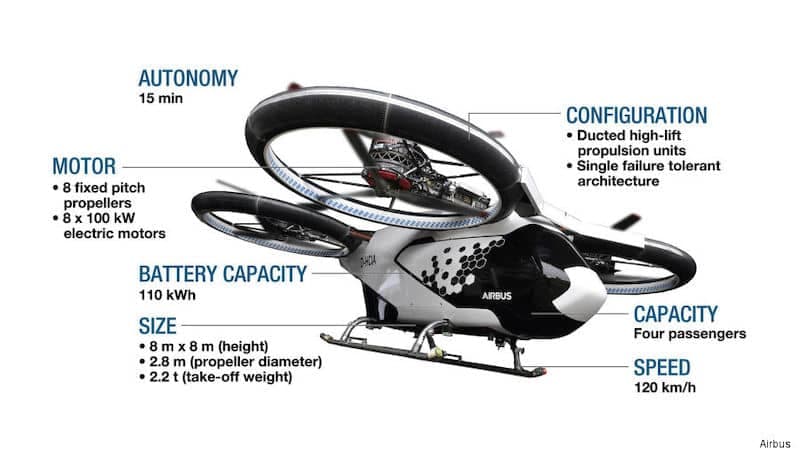
Multi-rotor wingless eVTOLs
The most basic type of eVTOL are multi-rotors, which are wingless vehicles that use horizontal rotors for lift and propulsion, similar to a large multicopter drone. An example is the Volocity from Volocopter which has 18 rotors, powered by individual motors. It’s 9 battery packs help it to achieve a top speed of 110kmh (68mph) and a range of 35km (22 miles) [4]. It is capable of carrying two passengers plus luggage. The arrangement of the rotors aids controllability and keeps them out of the way of the passengers.
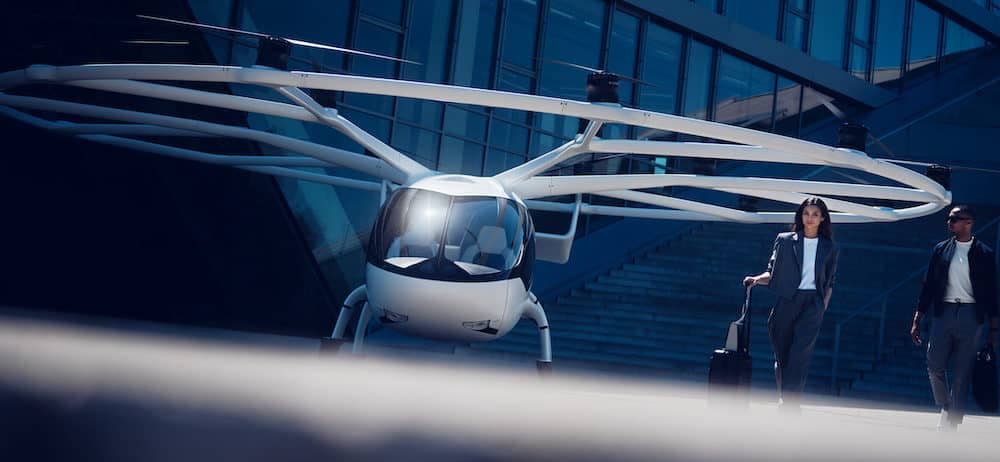
Lift and cruise eVTOLs
Multicopters are simple but require high power to remain in the air during forward flight as lift is only generated via propellors. Lithium-ion batteries have moved the boundaries on what is currently possible, but battery range is still a limitation. One approach to minimise this is to design eVTOLs with lift producing wings and propellers. This way, the vehicle can travel using a combination of battery power and lift, although a further set of rotors is required for vertical take-off and landing.
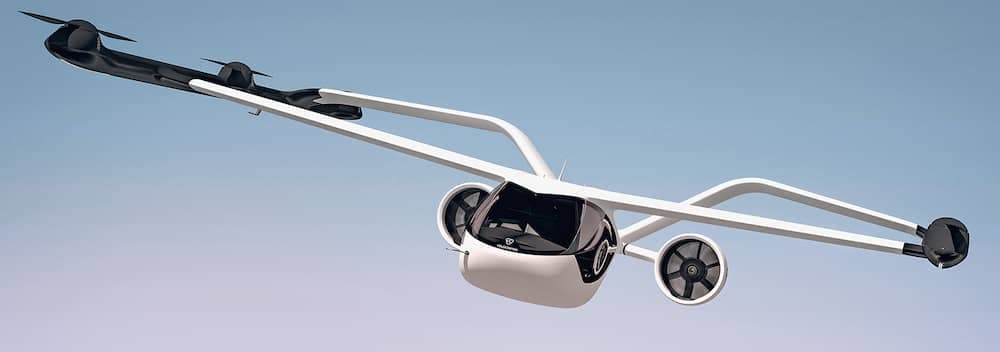
Vectored thrust eVTOLs
Winged aircraft solve many of the multicopter’s problems, but create some new ones too. The horizontal VTOL rotors are not efficient in level flight, creating a drag and weight penalty. However, this can be addressed by vectored thrust and tiltrotor vehicles. This is where the same rotors can be used to generate lift during vertical flight and then rotate to provide forward thrust during horizontal flight.
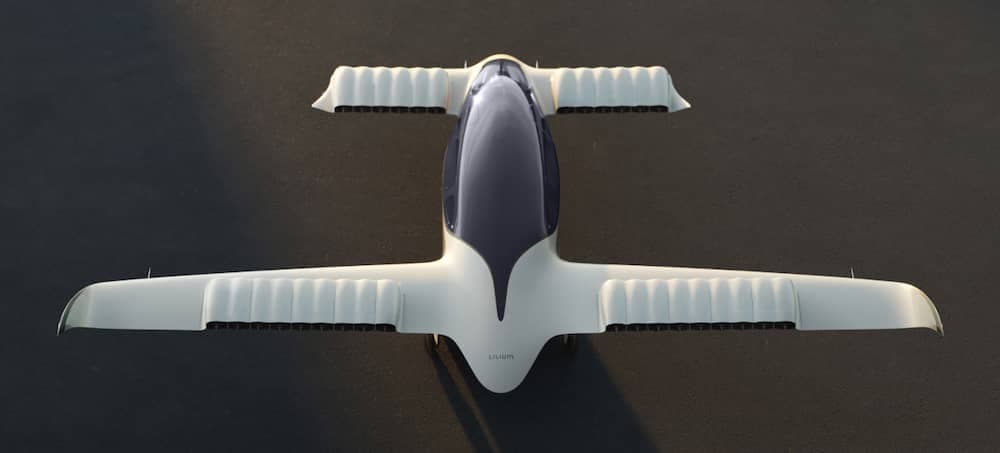
Urban air mobility certification
Before an eVTOL can take to the skies, it has to be fully certified to ensure it has been designed, manufactured and modified for safety throughout its life cycle. However, with UAM such a new concept, few regulations exist. Consequently, manufacturers and regulators such as the Federal Aviation Authority (FAA) in the USA, the European Union Aviation Safety Agency (EASA) in Europe and the Civil Aviation Authority (CAA) in the UK are working together to shape these regulations.
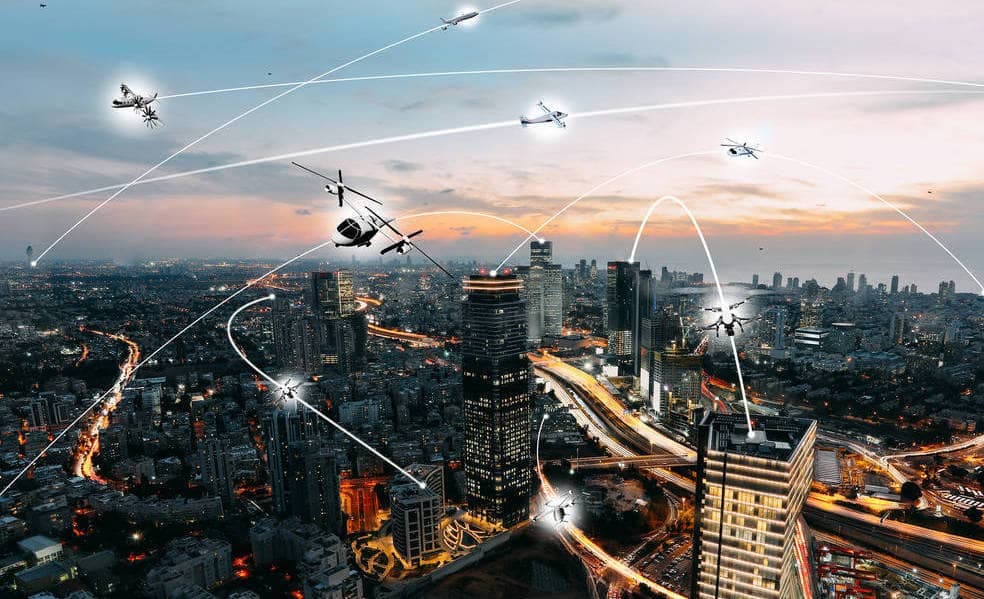
Joby Aviation were the first manufacturer to complete stage 4 G-1 certification from the FAA and airworthiness approval from the United States Airforce for its eVTOL aircraft. This concept uses pivoting rotors and conventional wings, much like the CV-22 Osprey tilt-rotor military cargo plane.
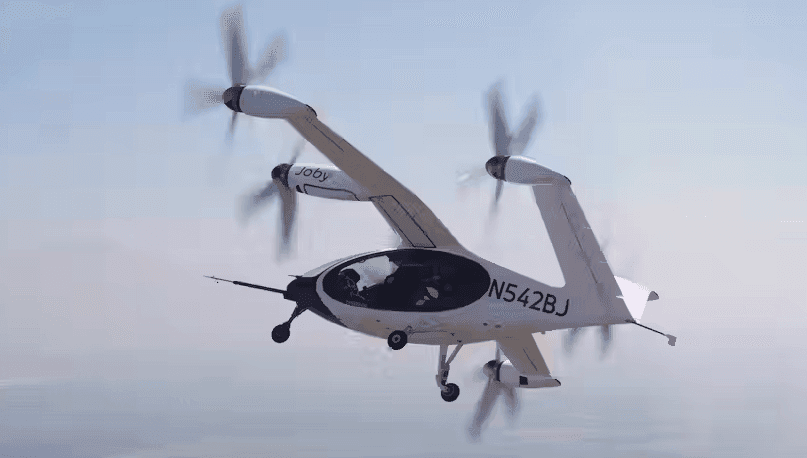
Developing an eVTOL powertrain
As UAM has moved from concept to reality, engineers have had to develop powertrains that satisfy the stringent power and weight criteria for this unique type of aircraft. Typically eVTOL powertrains consist of high voltage batteries that provide energy to electric motors which power the rotors.
However, vertical flight requires a substantial amount of energy and therefore a high energy dense battery. Some companies are aiming for a gravimetric battery energy density of around 450Wh/kg. For comparison, a typical EV battery has an energy density of approximately 250-450Wh/kg [3].
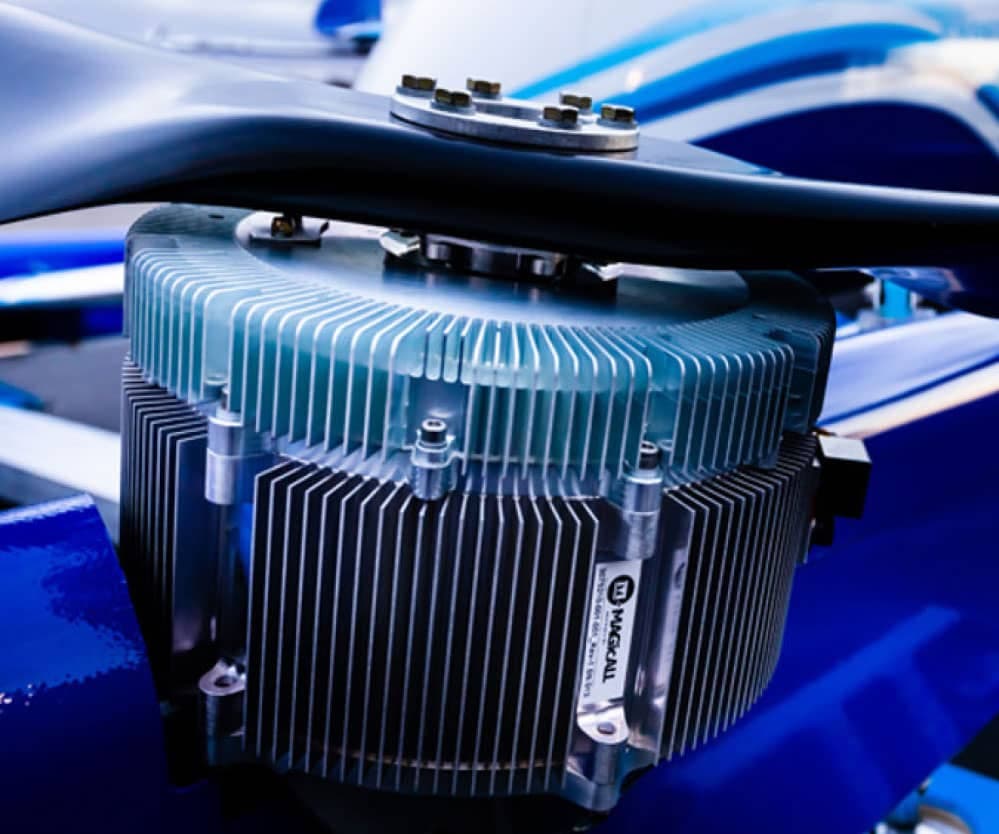
Unfortunately, energy dense batteries come with a weight penalty and this trade off between performance and payload is a constant headache for engineers. Consequently, advances in battery technology that enable higher power to weight ratio battery packs will bring the biggest performance gains to eVTOL aircraft.
Another challenge surrounding eVTOL powertrains is fast charging. Developing an eVTOL with the range and payload required for an air-taxi service is not practical without the ability to recharge quickly. The range of the battery is also of particular interest to the regulators and requires careful certification to ensure that commercial aircraft have sufficient energy reserves to divert to alternate landing sites if necessary.
Minimising eVTOL noise
The rotors are the final piece of the eVTOL powerplant puzzle and are key to payload, efficiency and noise. Noise might not be an obvious problem, but it is crucial to the success of urban air mobility. Previous forms of transport such as the Concorde failed to progress due to take-off noise and sonic boom problems over land. For eVTOLs, minimising noise is even more crucial as they will primarily operate over densely populated areas.
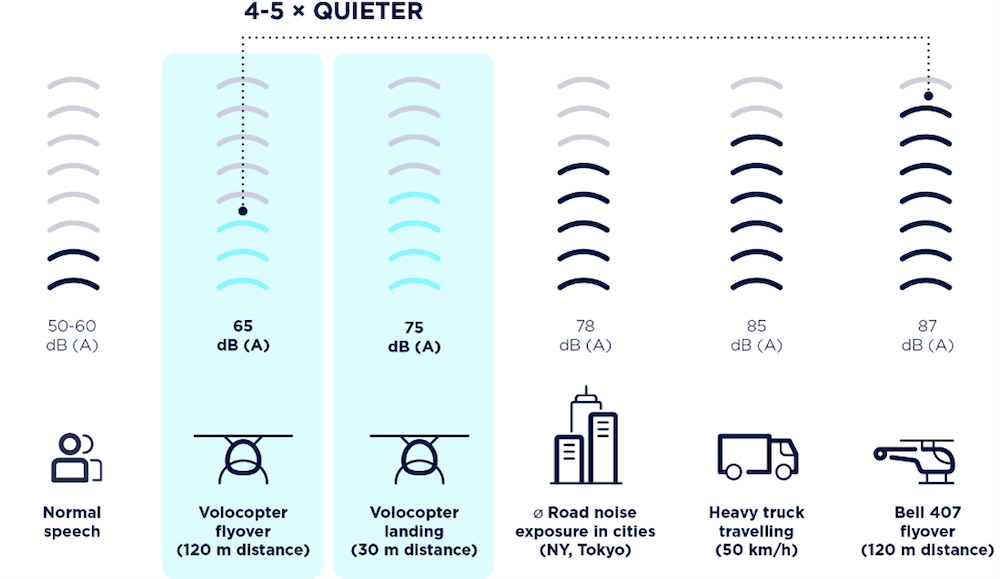
One of the key ways to reduce noise is to optimise the design of the rotors. As rotors rotate, the interaction between the blade vortex and the wake creates substantial noise. This is why helicopters, with their horizontal rotor layout are so loud when they fly overhead.
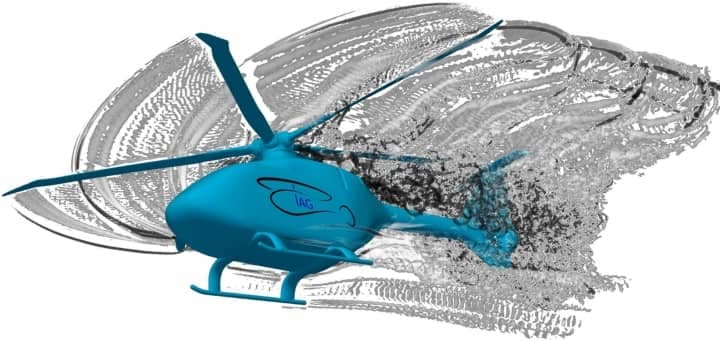
To improve the efficiency of the blades moving through air which will ultimately reduce the amount of wasted energy dissipated as noise, engineers aim to reduce disk loading. This is the ratio of weight per unit rotor area and is calculated by the below formula:
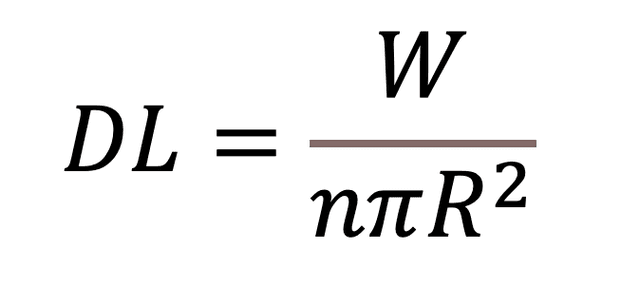
Where: DL = disk loading, W = total aircraft weight (kg), n = number of rotors, R = radius of the rotors
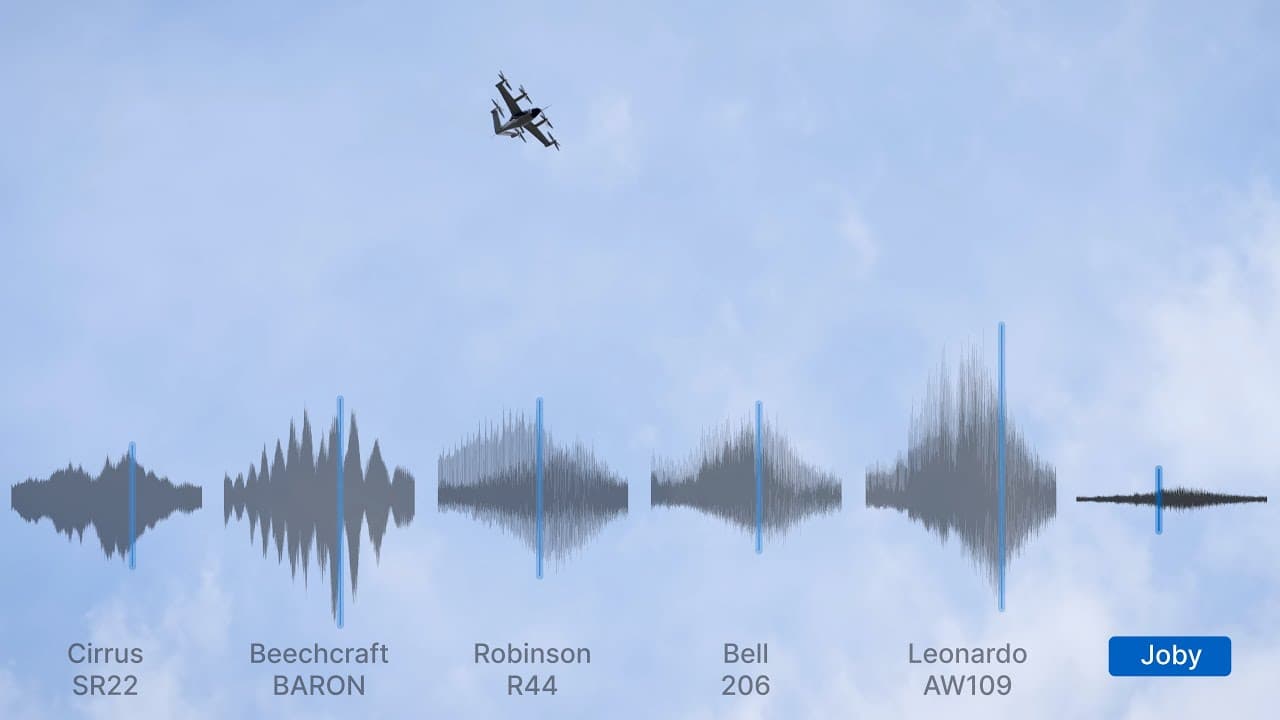
By reducing this value using multiple rotors along with optimising tip velocity, blade pitch, rotational speed and motor torque, the efficiency of the rotor can be improved and noise minimised. Furthermore, the use of ducted fans in eVTOL design eliminate the trailing rotor wake which not only increases efficiency and reduces noise, but also improves safety as there are no exposed rotors in close proximity to passengers.
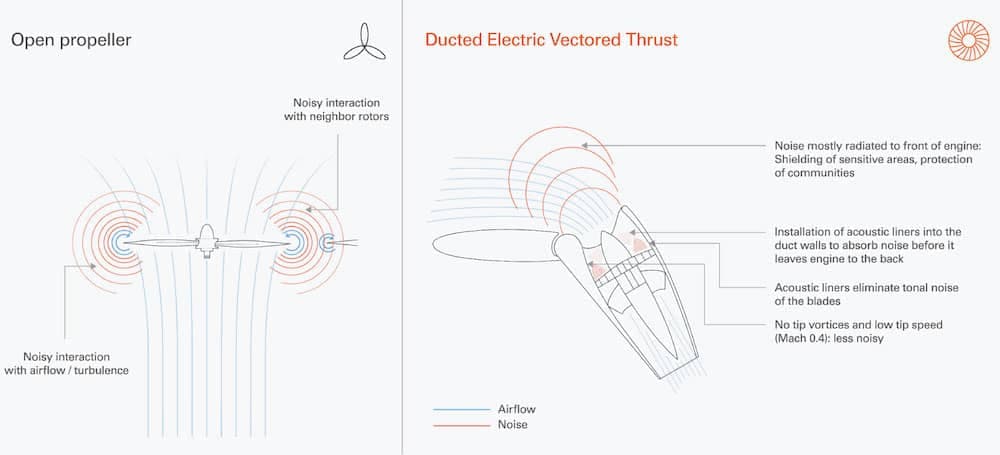
Vertiports
The co-operative nature of UAM development means that regulators, designers and infrastructure providers are all working together. This is particularly apparent in the design of vertiports, which have been defined by EASA as ‘an area of land, water or structure used or intended to be used for the landing and take-off of VTOL aircraft’.
These dedicated areas will provide the infrastructure to enable passengers and goods to be transported safely via eVTOLs. They will need to be easily accessible with good links to conventional travel networks and so will most likely be located at either existing airports or on rooftops within cities.
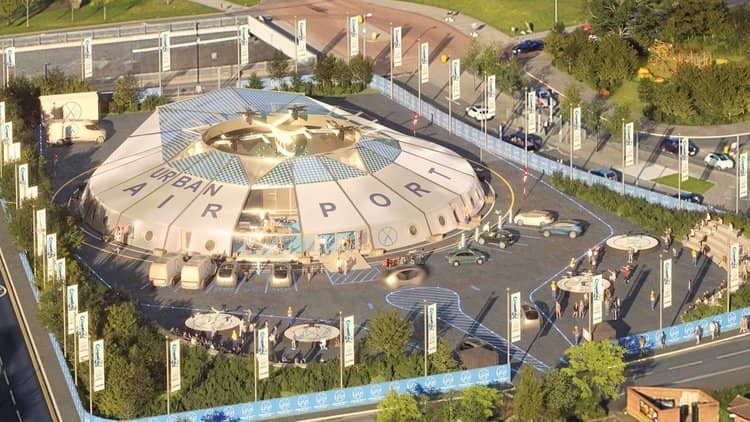
Improving eVTOL design with CFD
Many of the UAM projects currently in existence are paper exercises from tech start-ups looking for investment. With few physical aircraft, simulation is playing a vital role in the development of eVTOL design. This can range from simple spreadsheets to determine power and payload requirements to full CFD simulations of the entire aircraft.
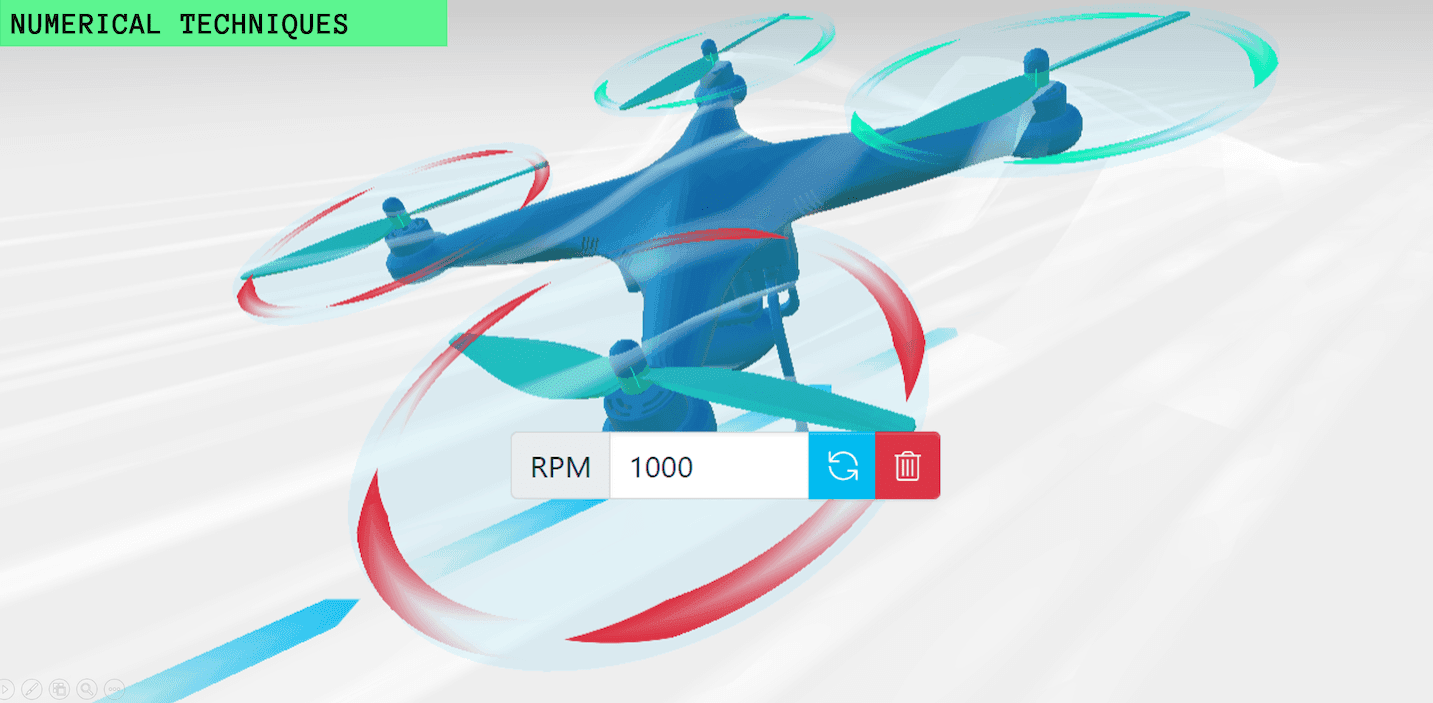
One of the most difficult aspects to design on tiltrotor or vectored thrust eVTOLs is the transition from hover to level flight. Computing power and CFD are not quite capable yet of simulating these relatively long transition events. Instead, multiple cases can be solved to cover all possible configurations. For those that have physical designs, wind tunnels can be used to test models, perhaps with active parts to truly study the moving elements.
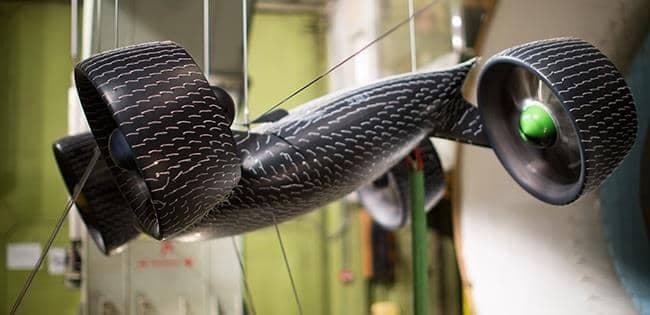
Time will tell whether the UAM concept and its eVTOLs are the 21st century flying cars or a true mobility solution revolution. But the race for the first eVTOL in the sky is accelerating the development of both eVTOL technology and aerodynamics. So keep your eyes on the skies because UAM eVTOLs could be flying sooner than you think.
Interesting links:
-
A NASA paper on UAM conceptual design
-
Rotor aerodynamic CFD video
-
Uber UAM white paper
-
UAM noise considerations and regulations
-
Quiet helicopter design
-
Lilium eVTOL design paper
References
[1] V.V., 2023. When–and where–will the first eVTOLs enter service?. [Online]. Aerotime Hub.
[2] 2019. London Assembly Average Traffic Speeds. [Online]. London.gov.
[3] 2019. New York city mobility report. [Online]. NYC Department of Transportation.
[4] 2019. Volocity Design specifications, August 2019. [Online]. Volocity.
[5] T.P., 2022. Cracking the Code for eVTOL Batteries. [Online]. Flying.