Introduction
Heavy Duty Vehicles (HDVs), which include trucks, buses, and coaches, account for more than 25% of greenhouse gas (GHG) emissions from road transport in the EU. They also contribute over 6% to the EU’s total GHG emissions. In line with the European Green Deal, the EU has adopted increasingly strict emission standards for HDVs to combat climate change.
CO2 Emission Reduction Targets
The EU introduced its first CO2 emission standards for heavy-duty vehicles in 2019. These regulations aimed to reduce the fleet-wide average CO2 emissions by 15% by 2025. However, amendments in 2024 expanded the scope of the regulations to include medium lorries, city buses, coaches, and trailers, with even more ambitious reduction targets:
- 15% reduction by 2025
- 45% reduction by 2030
- 65% reduction by 2035
- 90% reduction by 2040
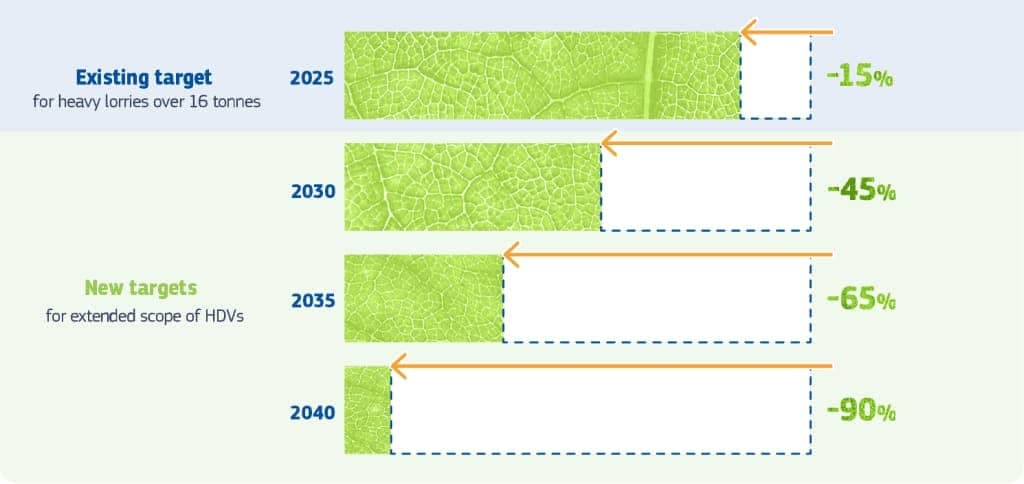
Specifically, starting in 2030, new semi-trailers must achieve a 10% reduction in CO2 emissions, while other new trailers must reach a 75% reduction.
Determining CO2 Emissions
To determine the CO2 emissions of a new vehicle, various performance metrics must be assessed, including:
- Rolling resistance
- Aerodynamic drag
- Masses and inertias
- Gearbox friction
- Auxiliary power
- Engine performance
These parameters are then input into the VECTO (Vehicle Energy Consumption Calculation Tool), which calculates the vehicle’s CO2 emissions under different usage scenarios.
For aerodynamics, manufacturers use the VECTO Airdrag tool, which calculates aerodynamic coefficients through road testing. Learn more about this process in our accompanying video.
The Role of CFD Simulations in VECTO
Aerodynamics of Trucks, Buses, and Coaches
During the design phase, CFD (Computational Fluid Dynamics) simulations play a vital role in understanding and optimizing the aerodynamics of trucks, buses, and coaches. These simulations allow manufacturers to digitally test multiple designs, significantly reducing the need for time-consuming and expensive prototype construction and wind tunnel testing.
While CFD simulations help optimize designs, real-world road testing is still mandatory for certification, as the EU requires emissions from HDVs to be tested under actual driving conditions. However, the EU is gradually increasing the use of CFD simulations to supplement or replace road testing for some vehicle variations, helping reduce certification costs and complexity.
Aerodynamics of Trailers
For trailers, manufacturers have more flexibility. They can rely solely on CFD methods to measure the aerodynamic gains of add-ons (such as tails or side skirts) without the need for physical road tests.
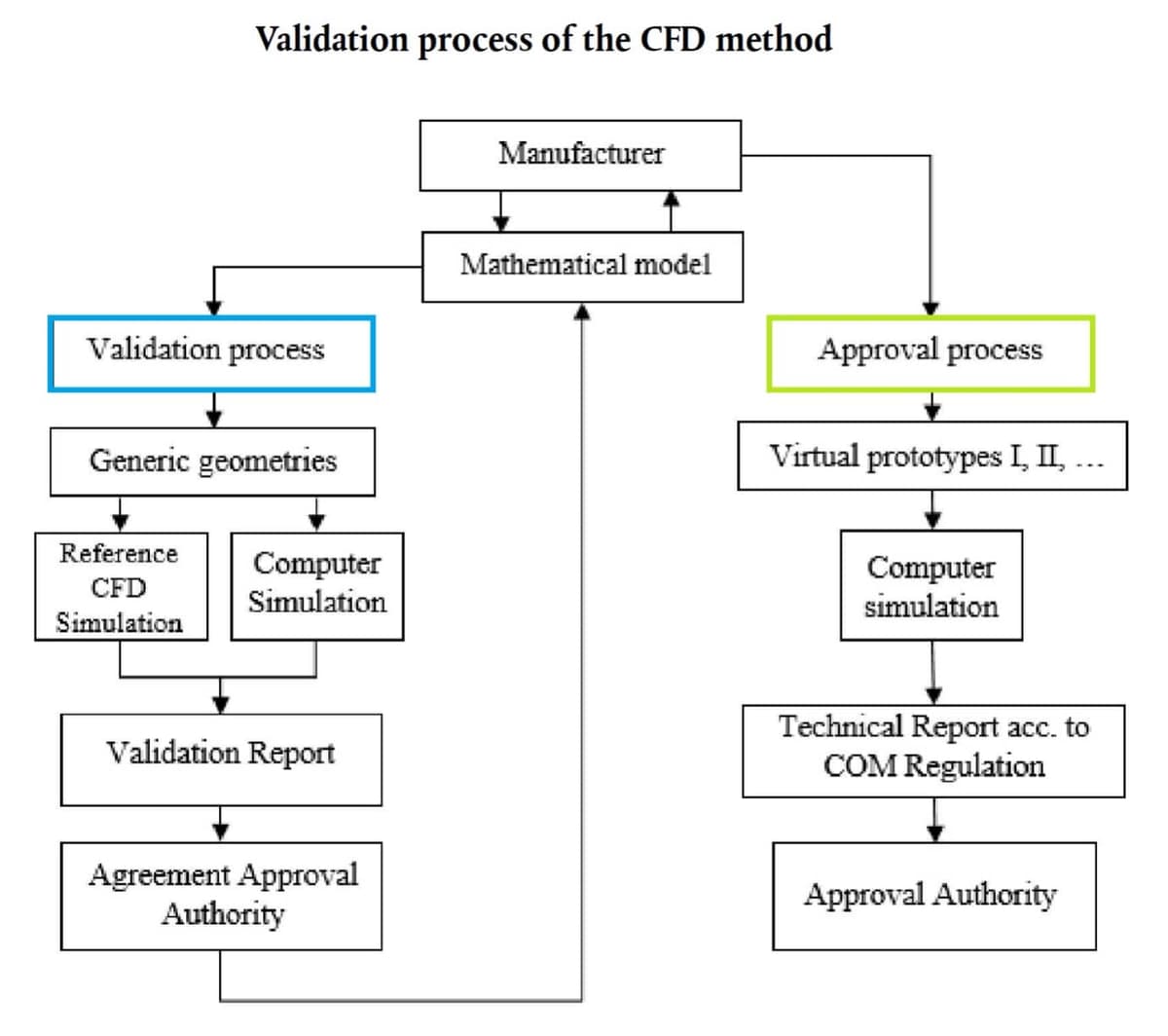
To certify their trailers, manufacturers must follow these two steps:
- Validation Process: Manufacturers must have their CFD methods validated by running simulations on benchmark geometries provided by the EU. This validation process must be documented and submitted to the appropriate approval authority.
- Approval Process: Once validated, the approved CFD method can be applied to the manufacturer’s specific trailers or trailer add-ons. The aerodynamic performance results are then submitted for final approval.
CFD Validation Process
Simulations
To validate your CFD method, you must conduct aerodynamic simulations on several reference geometries - the Base model, one with Long Side Covers (LSC) and one with Tall Rear Flaps (TRF). This must be done at three different yaw angles (0°, 3°, and 6°):
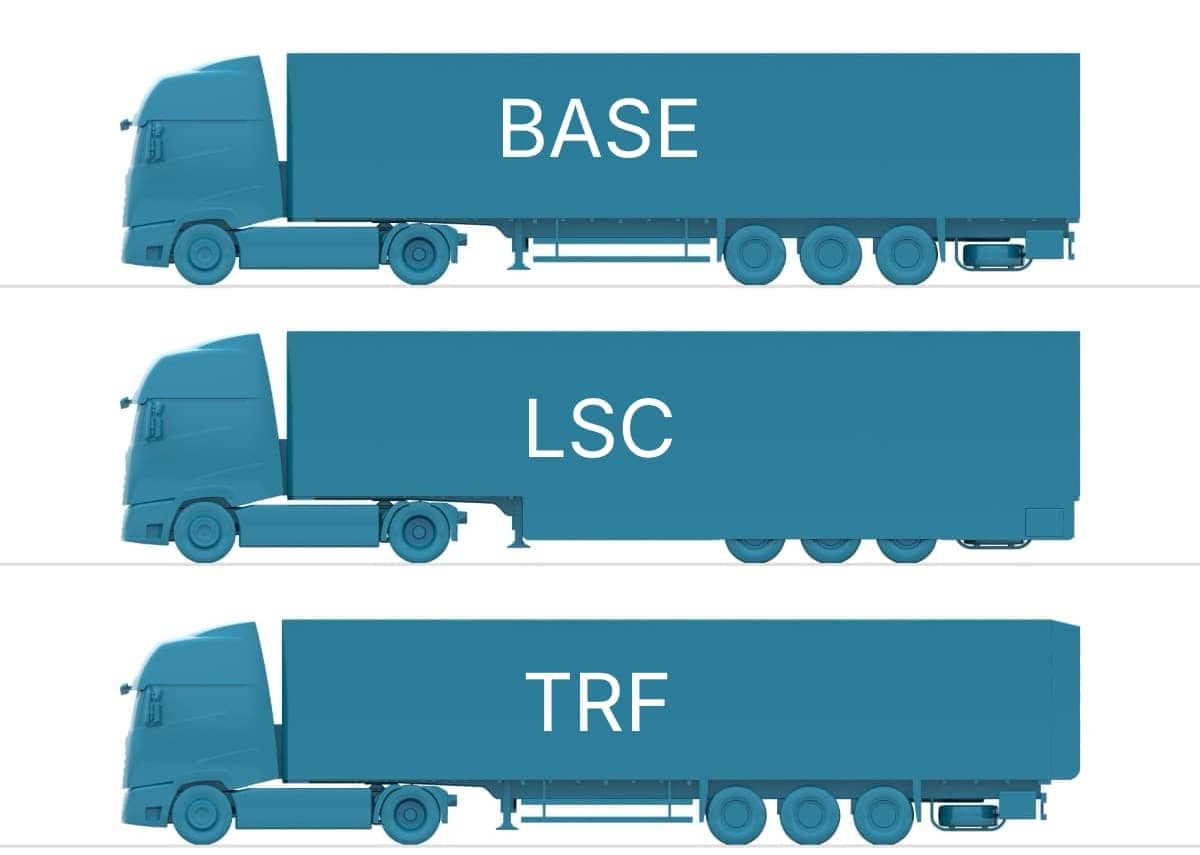
Several additional constraints must also be considered:
- Radiators: The pressure drop across the radiators must be modeled using porous elements that simulate airflow resistance.
- Domain Size: The virtual wind tunnel surrounding the truck must meet specific dimensions.
- Mesh Count: The simulation must include at least 60 million cells to ensure sufficient detail.
Validation
Once the simulations are complete, the drag reduction for each geometry and yaw angle must fall within defined error margins to meet approval requirements.
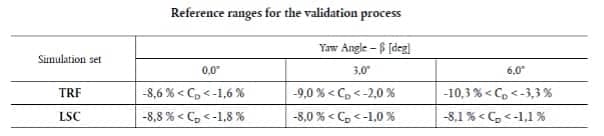
AirShaper’s CFD Expertise
At AirShaper, we’ve successfully performed these simulations using our Advanced CFD simulation, including rotating wheels and radiator modeling.
The images below show the pressure clouds (iso surface for a total pressure coefficient of 0) for the different geometries at a 3° yaw angle. You can observe how much smaller the wake is for the TRF configuration, as the flow is pulled down and inward by the tall rear flaps. Similarly, the flow around the rear wheels is cleaner and lower wake for the LSC is shorter, thanks to the shielding effect of the long side covers.
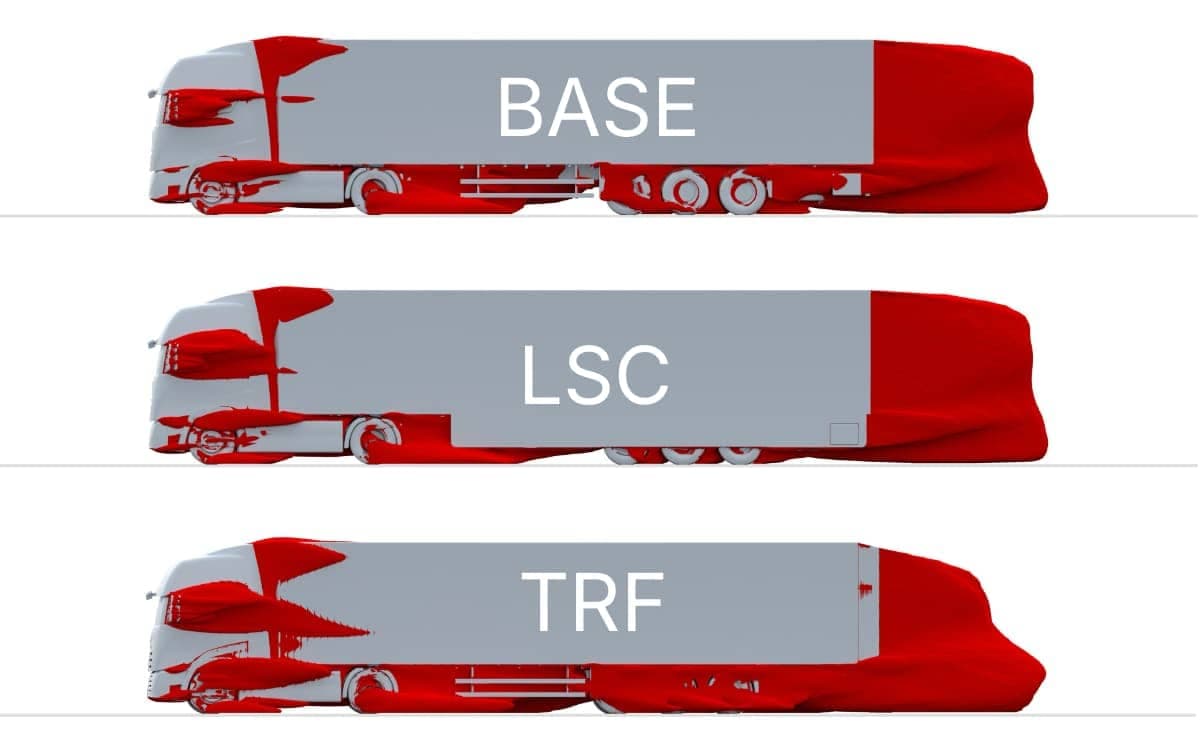
Our simulations fall within the required error bands, ensuring compliance with the validation process.
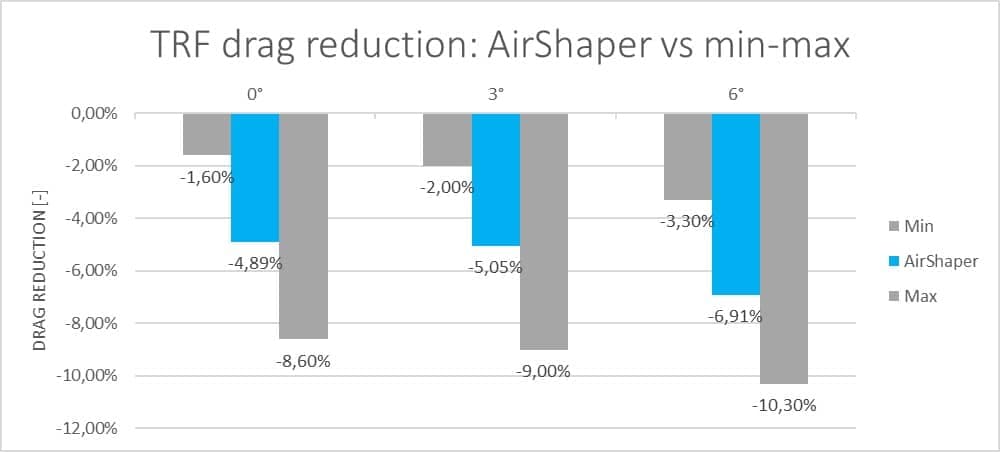
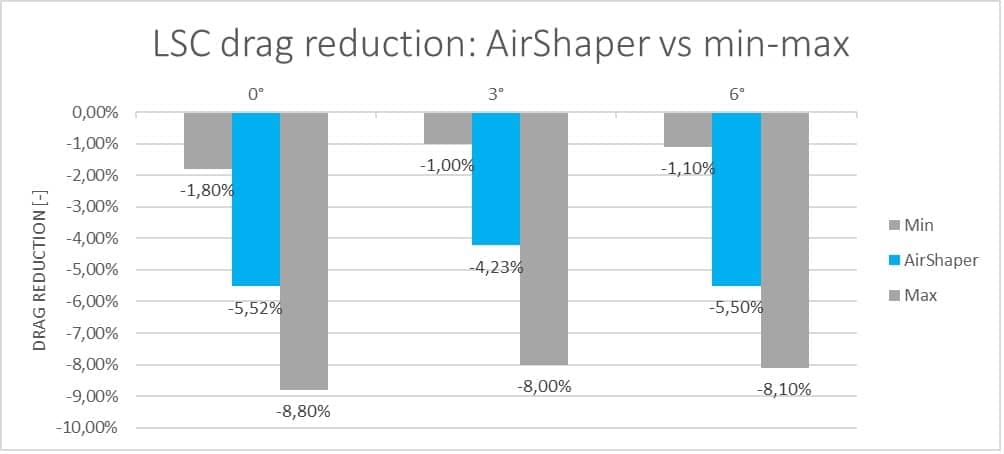
You can view the full simulation results here:
Configuration | 0° yaw | 3° yaw | 6° yaw |
---|---|---|---|
Base Model | Results | Results | Results |
LSC | Results | Results | Results |
TRF | Results | Results | Results |
Approval Process
Once validated, the same CFD method can be applied to 3D models of your trailer or add-ons. These simulations will predict drag reductions, which can then be input into the VECTO tool to calculate CO2 emissions. The results are compiled in a final report and submitted to the approval authority.
How AirShaper Can Help
AirShaper has extensive experience in optimizing the aerodynamics of various road vehicles, ranging from hyper efficient solar powered vehicles (like Aptera) and high performance race cars (like this 447.8 km/h custom Lamborghini) to drag reduction for heavy duty vehicles.
Specifically for projects within the framework of the EU CO2 emission reduction regulations, the AirShaper simulation methodology provides results which fall within the specified error bands. Additionally, AirShaper has a direct relationship with:
- Aerodynamic simulations to optimize drag reduction for trucks, buses, coaches, and trailers.
- Assistance with the CFD validation and approval process for trailers and trailer devices.
Additionally, we maintain direct relationships with:
- Manufacturers working on trucks, trailers, and add-ons
- Experts within the European Commission working on VECTO
- Accredited technical service providers such as TÜV Nord
- Technical support providers such as TU Graz (VECTO tool family, XML topics, related IT support)
If you’re developing vehicle aerodynamics solutions to meet EU regulations, AirShaper can provide the CFD expertise you need for a successful certification process.