Winglets are miniature vertical aerofoils found on the tips of an airplane wing. They may seem insignificant, but they are actually extremely powerful. Winglets minimise induced drag, improve fuel efficiency and result in around 6% fuel savings per plane. For an average Boeing 767 jet, that equates to a saving of over half a million gallons of jet fuel and 4,790 tonnes of CO2 per year.
The use of winglets doesn’t stop there - you can now find them on the tips of drone wings as well as wind turbine propeller blades. In fact, rear wing endplates on race cars are technically a type of winglet too. In each case, the winglets reduce the size of wingtip vortices and improve aerodynamic performance.
What are wingtip vortices?
A vortex is a rotating column of air, similar to a tornado. Vortices form behind any wing or body that generates positive or negative aerodynamic lift. In the case of an airplane wing, the total pressure below the wing is larger than the total pressure above the wing. This creates a net force upwards and is how an airplane wing generates lift.
However, air always wants to move from an area of high pressure to an area of low pressure. Therefore, air from the high pressure region below the wing spills over the tip of the wing and into the low pressure region above. This induces an angular velocity into the flow and as the air starts to turn, it can’t remain attached due to the trailing edge of the wing.
Consequently, the air continues to rotate, resulting in a column of air swirling inwards behind the tip of the wing. These rotating columns of air gradually dissipate downstream, as viscosity reduces the kinetic energy within the vortex.
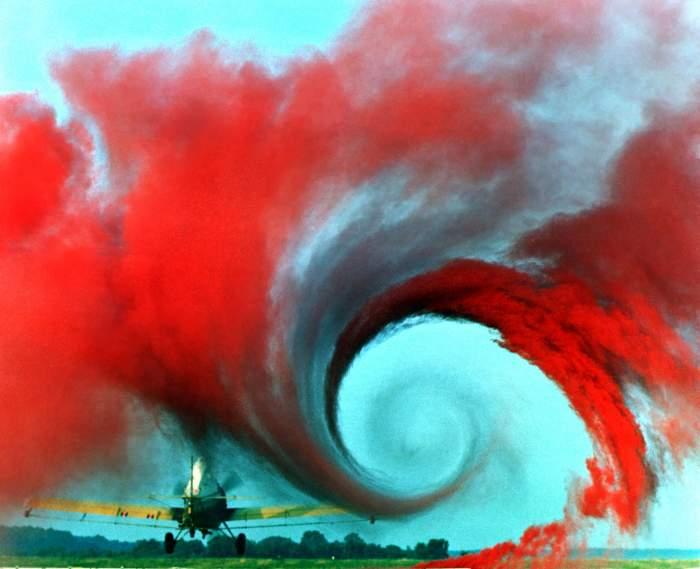
How do wingtip vortices contribute to drag?
Wingtip vortices cause additional downwash behind the wing. The resulting induced flow produces an additional force that faces downstream, which acts across the entire wing. This is known as induced drag or drag due to lift and is a three dimensional effect related to the distribution of lift across a wing.
Overall, this additional downwash reduces the effective angle of attack of the wing and ultimately, it’s lift coefficient. Therefore, to increase lift, the angle of attack needs to be increased. Unfortunately, this leads to an increase in induced drag. Flight dynamics of an airplane explained.
How do winglets work?
Induced drag is inversely proportional to the aspect ratio of a wing, so as aspect ratio increases, induced drag decreases. Aspect ratio is the square of the span divided by the wing area. Essentially, long, thin wings with a high aspect ratio have low induced drag; whereas thick, short wings have high induced drag.
This is because high aspect ratio wings are not as affected by wingtip vortices. The longer the wing, the further the tips are from the main portion of the wing so the reduction in lift due to wingtip vortices is less. Therefore, increasing the aspect ratio of wings by changing the wing geometry is one way to reduce the effect of wingtip vortices. Another way is to utilise winglets.
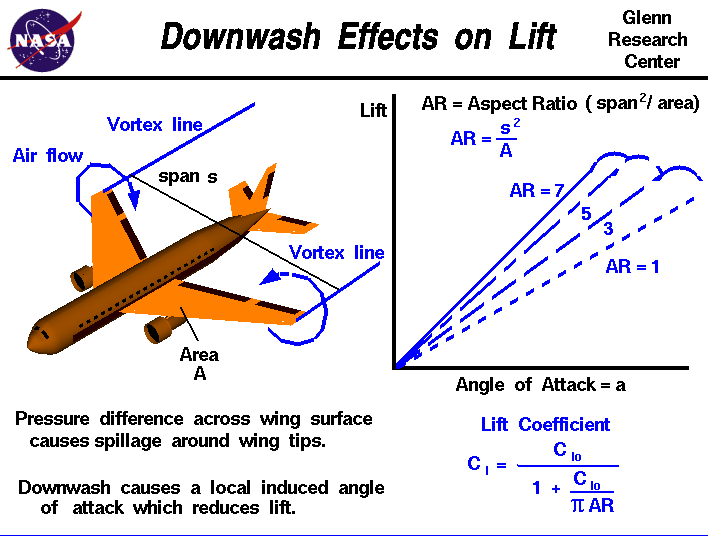
Winglets are small vertical planes that are added to the wing tips and generate a small portion of lift. They effectively act as a wall, preventing the air from the high pressure region below the wing crossing over to the low pressure area above the wing. Consequently, winglets manipulate the behaviour and reduce the strength of wingtip vortices. Effectively, this increases the aspect ratio of the wing, without modifying the wing’s geometry.
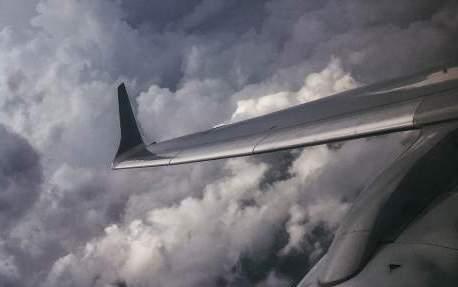
Blended winglets
The profile of the winglet and how it is integrated into the main wing has to be carefully designed to achieve the desired effect whilst minimising interference drag. The angle of the winglet to the main wing as well as the toe and its profile are all critical factors that affect the magnitude and orientation of its lift force.
As composite manufacturing techniques advanced, winglets can now be ‘blended’ into the main wing. This is where there is a smooth, curved transition with a large radius from the horizontal main wing to the vertical winglet. This was first investigated in the mid 1980s by Boeing and first installed on the Gulfstream II aircraft.

But how much can you really gain from adding winglets to a wing? We recently did a project on winglets for a fixed wing drone. Using AirShaper simulations, we analysed and refined the winglet design which improved the lift over drag ratio by up to 30%. This is a substantial gain for a fixed wing drone. See this article for more details.
Whatever the application, don’t underestimate the power of a well designed winglet. They may be small, but the aerodynamic benefits can be huge!