Different approaches
The aerodynamic design of small aeroplanes involves two main methods (prior to wind tunnel testing & flight testing). The first uses the theory of 2D airfoils, while the second focuses on 3D Computational Fluid Dynamics (CFD) simulations.
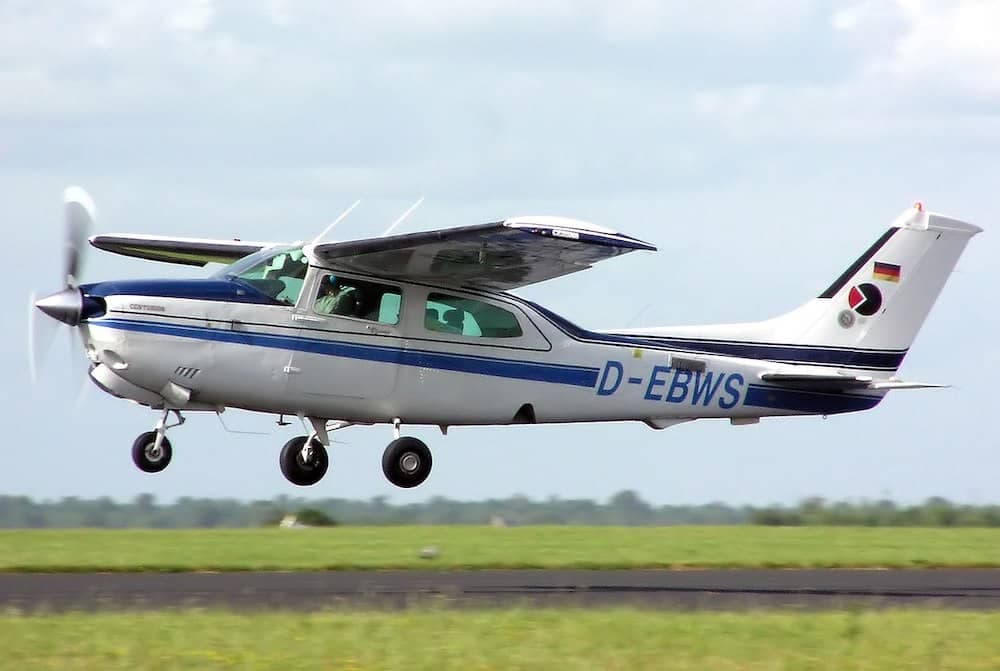
2D airfoil theory
Since 1915, when the Advisory Commission for Aeronautics was formed, 2D airfoils have been extensively researched and developed. This commission later became the National Advisory Commission for Aeronautics (NACA) and any airfoils created under this program were called NACA airfoils. Still today, aeroplane wings are often 3D extrusion elements based on 2D airfoils from the NACA database. Check out our guide to the best aerodynamic resources where you can find databases of airfoils, such as Airfoiltools.
3D CFD simulations
At the other end of the spectrum is 3D CFD. These are essentially simulations that capture the behaviour of airflow as it interacts with complex 3D objects. They are an excellent method of learning how much the flow deviates from the predicted 2D flow along a selected airfoil. These simulations can also be utilised to understand the intricate flow around other elements of an aeroplane such as the landing gear, cockpit and wing fuselage.
Lift off
An important aspect of determining the lift capacity of a wing based on 2D airfoils is the wing span. The 2D lift and drag properties of an airfoil are often provided for a section of an ‘infinitely wide’ wing. This means that end effects, such as wing tip vortices, where air crosses from high to low pressure via the side edge of the wing, are not taken into account. Therefore, the lift generated per unit length by a finite wing is much smaller than an infinite one, as the wing loading near the tips and even further away can be significantly reduced.
To counter this loss of lift, winglets can be implemented which, in their simplest form, are vertical flanges preventing the air from crossing and curling around the wing tip. This is relevant for all types and sizes of wing, even for fixed wing drones.
Increasing the flight time of a fixed wing drone case study
Optimization
To demonstrate that a small airplane can also benefit from optimized winglets, we used AirShaper’s Aerodynamic Shape Optimization software to optimize the winglets of a Cessna 210J Centurion.
We asked the software to morph the wing tip to improve the amount of lift generated by the wing and the results are shown below. The software designed a new 3D shape for the winglet which improved the lift of this section of wing by almost 60% with a minimal increase in drag.
--
As always with CFD simulations, the results need to be validated with wind tunnel or real world testing and at different angles of attack. There are also other factors such as manufacturing constraints and aesthetics that need to be evaluated before a design can be put into production. However, the software was able to optimize the complex 3D shape of a winglet quickly and robustly; providing an incredible tool that allows designers the freedom to create new, innovative and exciting shapes.